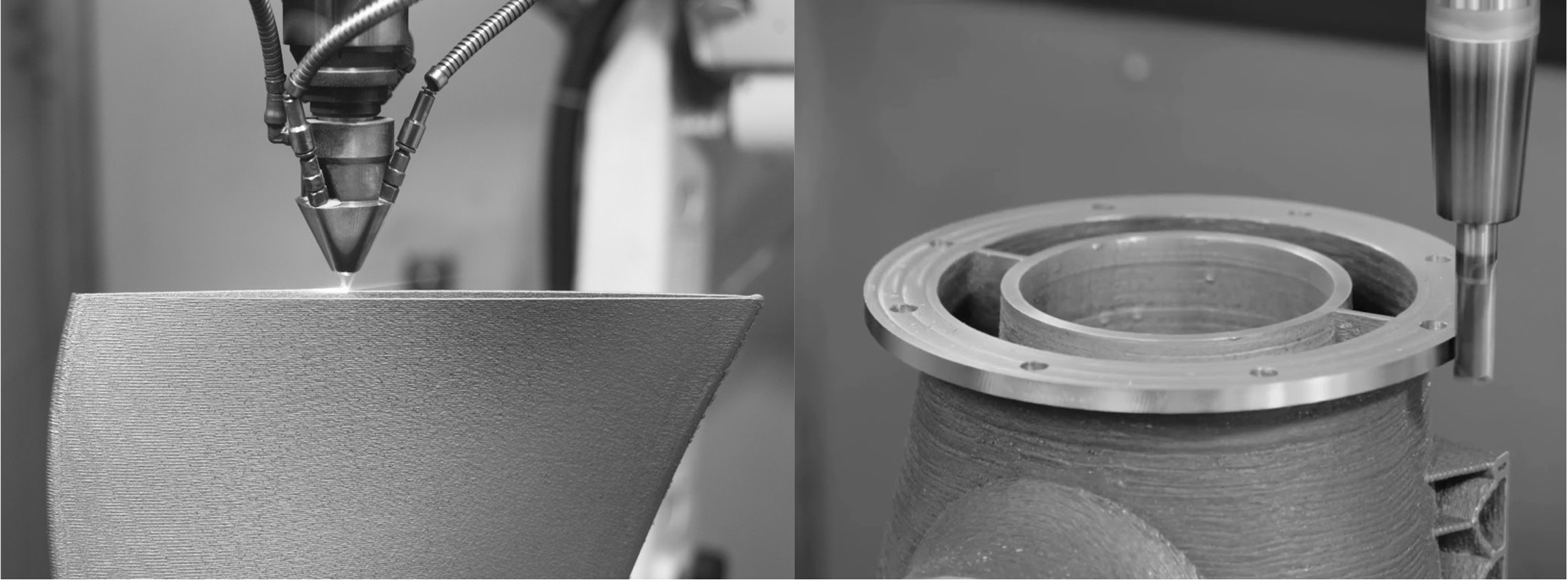
The manufacturing world is disrupted by newer technologies and additive manufacturing is one of them. AM can make complex designs that are entirely not possible by traditional technologies (CNC, injection molding etc)at much lower costs, however, AM lacks the potential of mass production. Conventional manufacturing is not going to be entirely replaced by the AM due to certain advantages offered by CM like mass manufacturing at lower cost and high precision components. The fusion of additive manufacturing and conventional manufacturing can create a hybrid manufacturing system that can leverage the best of both technologies. Complementing each other, a hybrid manufacturing system has the potential to unlock new opportunities across the wider industrial spectrum. Hybrid manufacturing can create precision products that are complex in design and shape with reduced wastage and costs.
Hybrid manufacturing system
AM made parts are sometimes machined to attain tighter tolerances and surface finish according to the need and it’s a known industry-wide practice. If both technologies are combined, then it is known as a hybrid manufacturing system. It means the same machine contains both additive and subtractive manufacturing capability. Currently, a CNC machine carves out the shape from the metal block as per the CAD the data and the removed material is just a waste. For expensive materials like titanium, alloy steel etc. it's a costly waste. Hybrid manufacturing is most suitable for the short-run production of metal components. There are machines available in the market which contains both additive and CNC marching set-up. Existing CNC machines can be retrofitted with addon AM capability like a retrofit AM system provided by a company called Hybrid Manufacturing Technologies.
To leverage the strength of the hybrid system, the designer should design the part suitable for this kind of manufacturing set-up. Initially, the AM system creates the shape which is known as the near-net-shape and is later machined by the CNC to carve out the final shape close to dimensional accuracy followed by post-processing according to the requirement. Or initially, the part is CNC machined and then features are created by AM system which is again CNC machined to required dimensional tolerances.
Photo credits: ResearchGate
Hybrid manufacturing technologies
Direct energy deposition
Direct energy deposition is an AM technology in which is the feedstock is either wire or powder which gets melted by the laser beam and simultaneously deposited on the build surface creating a near-net shape. Later machined by CNC to unravel the final shape as per CAD data with better surface quality and dimensional accuracy. Another way round, the part can be CNC machined initially and then features are created by the DED AM system which is again CNC machined to required dimensional tolerances. DED is most suitable for repairing damaged or broken parts and production of large metal components like rocket engines, nacelle etc.
DED Additive manufacturing
Cold spray
Cold spray is another AM technology where fine metals particles are sprayed at a very high speed on a built surface and fuse together to form a near-net shape. This AM process is suitable for softer materials like aluminium, copper etc. The particles are melted and fused together due to the heat generated by the kinetic energy hence no need for a laser beam system. Later, the part is CNC machined to achieve dimensional accuracy resulting in minimal wastage. This process is used for making large and lightweight metal parts for parts of the aerospace and automobile industry.
Cold Spray Additive manufacturing
Advantages of hybrid manufacturing
High metal flow rates
DED and cold spray create components in less time due to the high feedstock flow rate. Once AM process is done the part can immediately proceed to CNC machining resulting in reduced lead time for metal items.
High-density parts
High-density parts with precision can be created with hybrid manufacturing systems than the powder bed-based process. Additionally, these systems have multi-axis manufacturing capability to create parts in any direction without relying on supporting structures for overhang shapes.
Multi-material parts
The hybrid system can create multi-material parts with ease giving more freedom to the designers and enhancing the product performance. The performance will be the average of the two or more materials.
Complex and precision shapes
AM part of a hybrid manufacturing system can create complex geometries which cannot be made by CNC alone due to process limitations. Then, AM created complex geometry is machined to dimensional / profile accuracy. Hybrid manufacturing can create high-performance products which are extremely difficult to create with other manufacturing processes.
Application of hybrid manufacturing
Injection molding
Cores with conformal cooling channels can be made cost-effectively by a hybrid manufacturing system. AM can create the core with an inbuilt complex web of cooling channels which is later CNC machined to desired dimensional accuracy. Cores can be made in less time than the conventional manufacturing process and deliver a high rate of injection molding production by reducing the cycle time of the machine.
Aerospace Industry
A complex lightweight structure can be easily created by the hybrid manufacturing process. The multi-material capability could further enhance the performance of aerospace design. Aircraft fuel injectors and turbine blades are already made by AM processes.
Maintenance and Repair
Repair of critical parts with long production lead time, if ordered new, can be easily repaired to precision by hybrid manufacturing, hence, saving the costs and downtime for the industry.
Spare parts
On-time availability of spare parts is critical to certain industrial processes and, if the product is out of production, then it’s a serious concern. Hybrid manufacturing can help to get around this problem by producing the part at a fraction of the cost and time. And no inventory holding costs because parts can be produced on-demand according to the need.
Conclusion
Hybrid manufacturing is a recent introduction and has the potential for limitless possibilities for the manufacturing industries. The ability to produce lightweight and complex parts with precision which is not possible to make by conventional manufacturing process will transform the entire industry from shorter lead time to a simplified supply chain and cost-saving.
Blog created by - 3D SculpLab Team