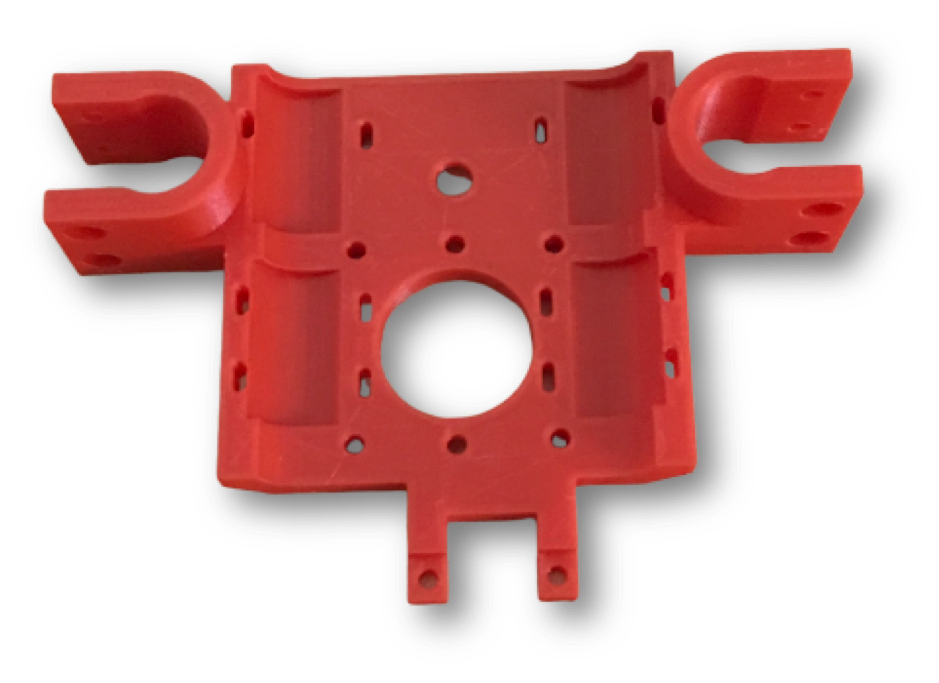
Wide material options for your requirements
Tensile modulus | 2346 MPa |
Tensile stress at yield | 38 MPa |
Tensile stress at break | 36 MPa |
Elongation at yield | 2.10% |
Elongation at break | 2.84% |
Flexural strength | 65.7 MPa |
Flexural modulus | 2409 MPa |
Hardness | 83 Shore D |
Max Working temp. | Upto 60˚C |
Price | TBD |
Lead Time | ~2 days |
Min. Wall Thickness (Recommended) | 1.2 mm |
Tolerances | ±0.5mm |
Max part size | 300x300x300mm |
Layer height | 100 - 250 microns |
Disclaimer - Material properties are for general-purpose reference only and have been made available on a best effort basis for the users as a quick information guide for the material selection.
Tensile modulus | 1820 MPa |
Tensile stress at yield | 37 MPa |
Tensile stress at break | 37 MPa |
Elongation at yield | 3.10% |
Elongation at break | 3.10% |
Flexural strength | 78 MPa |
Flexural modulus | 2490 MPa |
Hardness | 79 Shore D |
Max Working temp. | Upto 60˚C |
Price | TBD |
Lead Time | ~2 days |
Min. Wall Thickness (Recommended) | 1.2 mm |
Tolerances | ±0.5mm |
Max part size | 200x200x200mm |
Layer height | 100 - 250 microns |
Disclaimer - Material properties are for general-purpose reference only and have been made available on a best effort basis for the users as a quick information guide for the material selection.
Key features -
Mechanical properties -
Tensile modulus | 1681 MPa |
Tensile stress at yield | 39 MPa |
Tensile stress at break | 33 MPa |
Elongation at yield | 3.50% |
Elongation at break | 4.80% |
Flexural strength | 70 MPa |
Flexural modulus | 2070 MPa |
Hardness | 76 Shore D |
Thermal properties -
Max Working temp. | Upto 85˚C |
Other info -
Price | TBD |
Lead Time | ~2 days |
Min. Wall Thickness (Recommended) | 1.2 mm |
Tolerances | ±0.5mm |
Max part size | 200x200x200mm |
Layer height | 100 - 250 microns |
Disclaimer - Material properties are for general-purpose reference only and have been made available on a best effort basis for the users as a quick information guide for the material selection.
Tensile modulus | 1904 MPa |
Tensile stress at break | 53.7 MPa |
Elongation at break | 5.90% |
Flexural strength | 95 MPa |
Flexural modulus | 2310 MPa |
Hardness | 80 Shore D |
Max Working temp. | Upto 110˚C |
Price | TBD |
Lead Time | ~2 days |
Min. Wall Thickness (Recommended) | 1.2 mm |
Tolerances | ±0.5mm |
Max part size | 200x200x200mm |
Layer height | 100 - 250 microns |
Disclaimer - Material properties are for general-purpose reference only and have been made available on a best effort basis for the users as a quick information guide for the material selection.
Tensile modulus | 1537 MPa |
Tensile stress at yield | 41 MPa |
Tensile stress at break | 37.7 MPa |
Elongation at yield | 4.70% |
Elongation at break | 5.10% |
Flexural strength | 79 MPa |
Flexural modulus | 1990 MPa |
Hardness | 72 Shore D |
Max Working temp. | Upto 70˚C |
Price | TBD |
Lead Time | ~2 days |
Min. Wall Thickness (Recommended) | 1.2 mm |
Tolerances | ±0.5mm |
Max part size | 200x200x200mm |
Layer height | 100 - 250 microns |
Disclaimer - Material properties are for general-purpose reference only and have been made available on a best effort basis for the users as a quick information guide for the material selection.
Tensile modulus | 26 MPa |
Tensile stress at yield | 8.6 MPa |
Tensile stress at break | 39 MPa |
Elongation at yield | 55% |
Elongation at break | 580% |
Flexural strength | 4.3 MPa |
Flexural modulus | 78.7 MPa |
Hardness | 95 Shore D |
Max Working temp. | Upto 100˚C |
Price | TBD |
Lead Time | ~2 days |
Min. Wall Thickness (Recommended) | 1.2 mm |
Tolerances | ±0.5mm |
Max part size | 200x200x200mm |
Layer height | 100 microns |
Disclaimer - Material properties are for general-purpose reference only and have been made available on a best effort basis for the users as a quick information guide for the material selection.
Tensile modulus | 220 MPa |
Tensile stress at yield | 8.7 MPa |
Elongation at yield | 18% |
Elongation at break | >300% |
Flexural strength | 13 MPa |
Flexural modulus | 305 MPa |
Hardness | 45 Shore D |
Max Working temp. | Upto 105˚C |
Price | TBD |
Lead Time | ~2 days |
Min. Wall Thickness (Recommended) | 1.2 mm |
Tolerances | ±0.5mm |
Max part size | 200x200x200mm |
Layer height | 100 - 250 microns |
Disclaimer - Material properties are for general-purpose reference only and have been made available on a best effort basis for the users as a quick information guide for the material selection.
Elongation at break | 6% |
Flexural strength | 41 MPa |
Hardness | 46 Shore D |
Max Working temp. | Upto 60˚C |
Price | TBD |
Lead Time | ~2 days |
Min. Wall Thickness (Recommended) | 1.2 mm |
Tolerances | ±0.5mm |
Max part size | 200x200x200mm |
Layer height | 100 - 250 microns |
Disclaimer - Material properties are for general-purpose reference only and have been made available on a best effort basis for the users as a quick information guide for the material selection.
Nylon is a non-abrasive material that is good for ergonomic shapes and holding fixtures for parts that are easily scratched. It can be painted or dyed.
Tensile modulus (Young Mod) | 1.7 GPa |
Tensile stress at yield | 51 MPa |
Tensile stress at break | 36 MPa |
Elongation at break | 150% |
Flexural strength | 50 MPa |
Flexural modulus | 1.4 GPa |
Izod Impact - notched (J/m) | 110 J/m |
Density | 1.1 g/cm3 |
Max Working temp. | Upto 60˚C |
Price | TBD |
Lead Time | 2~3 days |
Min. Wall Thickness (Recommended) | 1mm |
Tolerances | ±0.5mm |
Max part size | 200x200x200mm |
Layer height | 100 microns |
Disclaimer - Material properties are for general-purpose reference only and have been made available on a best effort basis for the users as a quick information guide for the material selection.
Tensile modulus | 2290 MPa |
Tensile stress at break | 46 MPa |
Elongation at break | 8% |
Flexural strength | 74 MPa |
Flexural modulus | 2040 MPa |
Hardness | 86 Shore D |
Max Working temp. | Upto 60˚C |
Price | TBD |
Lead Time | ~2 days |
Min. Wall Thickness (Recommended) | 0.8 mm |
Tolerances | ±0.5mm |
Max part size | 145x145x175mm |
Layer height | 100 microns |
Disclaimer - Material properties are for general-purpose reference only and have been made available on a best effort basis for the users as a quick information guide for the material selection.
Tensile modulus | 1650 MPa |
Tensile strength | 48 Mpa |
Elongation at break | 18% |
Flexural strength | 41 Mpa |
Flexural modulus | 1500 Mpa |
Hardness | 75 Shore D |
Heat deflection temp (Td) | 86˚C |
Lead Time | ~3 days |
Wall Thickness | 1mm |
Tolerances | ±0.5mm |
Max part size | 300×300×500mm |
Layer height | 150 microns |
Disclaimer - Material properties are for general-purpose reference only and have been made available on a best effort basis for the users as a quick information guide for the material selection.
Aluminum (AlSi10Mg) is a typical casting alloy with good casting properties and is typically used for cast parts with thin walls and complex geometry. It offers good strength, hardness and dynamic properties and is therefore also used for parts subject to high loads. Aluminium AlSi10Mg is ideal for applications that require a combination of good thermal properties and low weight. They can be machined, spark-eroded, welded, micro shot-peened, polished and coated if required.
Tensile modulus | 70 GPa (x-y-z dir.) |
Tensile strength | 390 MPa (x-y dir.) & 390MPa (z dir.) |
Tensile stress at yield | 220 MPa (x-y dir.) & 210MPa (z dir.) |
Elongation at break | 8% (x-y dir.) & 6% (z dir.) |
Price | TBD |
Lead Time | 3~4 days |
Wall Thickness | 1mm |
Tolerances | See below |
Max part size | 250×250×300mm |
Layer height | 100 microns |
Disclaimer - Material properties are for general-purpose reference only and have been made available on a best effort basis for the users as a quick information guide for the material selection.
ABS-M30 is stronger than standard ABS, making it ideal for prototyping, concept evaluation, functional parts, manufacturing aids etc.
Tensile modulus | 2.4 GPa |
Tensile stress at yield | 30 MPa |
Tensile stress at break | 28 MPa |
Elongation at yield | 1.80% |
Elongation at break | 8% |
Flexural modulus | 2.2GPa |
Price | TBD |
Lead Time | 2~3 days |
Wall Thickness | 1mm |
Tolerances | ±0.5mm |
Max part size | 400x350x400 |
Layer height | 150 microns |
Disclaimer - Material properties are for general-purpose reference only and have been made available on a best effort basis for the users as a quick information guide for the material selection.
ASA (Acrylonitrile Styrene Acrylate). It is similar to ABS but with better UV resistance, mechanical properties and aesthetics than ABS. ASA is suitable for general-purpose prototyping, jigs and fixtures, short-run production parts and outdoor applications.
Tensile modulus | 2.14GPa |
Tensile stress at yield | 32MPa |
Tensile stress at break | 31MPa |
Elongation at yield | 2.50% |
Elongation at break | 5.90% |
Flexural modulus | 1.98GPa |
Price | TBD |
Lead Time | 2~3 days |
Wall Thickness | 1mm |
Tolerances | ±0.5mm |
Max part size | 400x350x400 |
Layer height | 150 microns |
Disclaimer - Material properties are for general-purpose reference only and have been made available on a best effort basis for the users as a quick information guide for the material selection.
Accura 25 (another name VisiJet® SL Flex) provides the polypropylene-like look and feel and white opaque colour with high flexibility. The part retains its shape and is generally suitable for snap-fits assemblies.
Tensile modulus | 1.6GPa |
Tensile strength | 38MPa |
Elongation at break | 16% |
Flexural strength | 57MPa |
Flexural modulus | 1.4GPa |
Hardness | 80 Shore D |
Heat deflection temp (Td) | 60˚C |
Price | TBD |
Lead Time | ~2 days |
Wall Thickness | 0.5mm |
Tolerances | ±0.1mm |
Max part size | 380x380x250mm |
Layer height | 100 microns |
Disclaimer - Material properties are for general-purpose reference only and have been made available on a best effort basis for the users as a quick information guide for the material selection.
Rigid material (Figure 4® PRO-BLK) is a high precision resin producing parts with a smooth surface finish and sidewall quality and has excellent mechanical properties.
Tensile modulus | 2.3GPa |
Tensile strength | 63MPa |
Tensile stress at yield | 63MPa |
Elongation at yield | 4.70% |
Elongation at break | 12% |
Flexural strength | 92MPa |
Flexural modulus | 2.2GPa |
Hardness | 79 Shore D |
Heat deflection temp (Td) | 70˚C |
Price | TBD |
Lead Time | ~2 days |
Wall Thickness | 0.5mm |
Tolerances | ±0.1mm |
Max part size | 124x70x196mm |
Layer height | 100 microns |
Disclaimer - Material properties are for general-purpose reference only and have been made available on a best effort basis for the users as a quick information guide for the material selection.
Titanium (Ti6Al4V) has an excellent strength to weight ratio that makes it the right choice where lightweight loading structures are needed. It is also biocompatible, so can be used across a wide range of surgical and dental applications. It has good corrosion resistance.
Tensile modulus (Young Mod) | 132 GPa (x-y dir.) & 128 GPa (z dir.) |
Tensile strength (UTM) | 1091 MPa (x-y dir.) & 1084 MPa (z dir.) |
Tensile stress at yield | 1020 MPa (x-y dir.) & 987 MPa (z dir.) |
Elongation at break | 16% (x-y dir.) & 17% (z dir.) |
Hardness | 363 Vickers |
Melting temperature | 1635˚C |
Thermal conductivity | 6 W/mK to 8 W/mK |
Thermal expansion coefficient | 8x10-6 K-1 to 9x10-6 K-1 |
Density | 4.42 g/cm3 |
Price | TBD |
Lead Time | 3~4 days |
Wall Thickness | 0.5mm |
Tolerances | See below |
Max part size | 250×250×300mm |
Layer height | 100 microns |
Disclaimer - Material properties are for general-purpose reference only and have been made available on a best effort basis for the users as a quick information guide for the material selection.
Onyx (Strong Nylon) is a micro carbon fibre-filled nylon that yields accurate parts with a near-flawless surface finish. It offers high strength, toughness, and chemical resistance. Additional strength can also be achieved by reinforcing it with fibres like carbon fiber, glass fiber, HSHT Glass fiber & kevlar to yield aluminium-strength parts.
Tensile modulus (Young's Mod) | 2.4 GPa |
Tensile stress at yield | 40 MPa |
Tensile stress at break | 37 MPa |
Elongation at break | 25% |
Flexural strength | 71 MPa |
Flexural modulus | 3 GPa |
Izod Impact - notched | 330 J/m |
Heat deflection temp (Td) | 145˚C |
Density | 1.2 g/cm3 |
Price | TBD |
Lead Time | 2~3 days |
Wall Thickness | 1mm |
Tolerances | ±0.5mm |
Max part size | 330×270×200mm |
Layer height | 100 microns |
Disclaimer - Material properties are for general-purpose reference only and have been made available on a best effort basis for the users as a quick information guide for the material selection.
Onyx FR is a flame-retardant variant of Onyx(strong nylon) designed for use in applications where parts must be non-flammable. Additional strength can also be achieved by reinforcing it with fibers like carbon fiber, glass fiber, HSHT Glass fiber & kevlar to yield aluminium-strength parts.
Tensile modulus (Young Mod) | 3.0 GPa |
Tensile stress at yield | 41 MPa |
Tensile stress at break | 40 MPa |
Elongation at break | 18% |
Flexural strength | 71 MPa |
Flexural modulus | 3.6 GPa |
Heat deflection temp (Td) | 145˚C |
Density | 1.2 g/cm3 |
Price | TBD |
Lead Time | 2~3 days |
Wall Thickness | 1mm |
Tolerances | ±0.5mm |
Max part size | 330×270×200mm |
Layer height | 100 microns |
Disclaimer - Material properties are for general-purpose reference only and have been made available on a best effort basis for the users as a quick information guide for the material selection.
Onyx ESD is a static-dissipative with micro carbon fibre-filled nylon material, precision-engineered for a tight range of surface resistance. Onyx ESD meets ESD-safe requirements of the most stringent manufacturing needs. Onyx ESD is stronger and stiffer than Onyx(Strong Nylon), with the same near-perfect surface finish, making it suitable for advanced manufacturing applications from electronics assembly, industrial robotics and process automation.
Tensile modulus (Young Mod) | 4.2 GPa |
Tensile stress at yield | 52 MPa |
Tensile stress at break | 50 MPa |
Elongation at break | 25% |
Flexural strength | 83 MPa |
Flexural modulus | 3.7 GPa |
Izod Impact - notched (J/m) | 44 J/m |
Heat deflection temp (Td) | 138˚C |
Density | 1.2 g/cm3 |
Price | TBD |
Lead Time | 2~3 days |
Wall Thickness | 1mm |
Tolerances | ±0.5mm |
Max part size | 330×270×200mm |
Layer height | 100 microns |
Disclaimer - Material properties are for general-purpose reference only and have been made available on a best effort basis for the users as a quick information guide for the material selection.
Carbon Fiber is a unique, ultra-high-strength material when laid into a base material like Onyx(Strong Nylon), it can create parts as strong as 6061-T6 Aluminum or even substitute it. It’s extremely stiff and strong and can be laid down in a wide variety of geometries.
Tensile Strength | 800 MPa |
Tensile Modulus | 60 GPa |
Tensile Strain at Break | 1.50% |
Flexural Strength | 540 MPa |
Flexural Modulus | 51 GPa |
Flexural Strain at Break | 1.20% |
Compressive Strength | 420 MPa |
Compressive Modulus | 62 GPa |
Compressive Strain at Break | 0.70% |
Heat Deflection Temp | 105˚C |
Izod Impact - notched | 960 J/m |
Density | 1.4 g/cm3 |
Price | TBD |
Lead Time | 2~3 days |
Wall Thickness | 1mm |
Tolerances | ±0.5mm |
Max part size | 330×270×200mm |
Layer height | 100 microns |
Disclaimer - Material properties are for general-purpose reference only and have been made available on a best effort basis for the users as a quick information guide for the material selection.
GlassFiber is an entry-level fiber material capable of producing parts 10x stronger than ABS when laid into a base material like Onyx(Strong Nylon). Glass fiber provides a more affordable alternative to carbon fiber. Glass fiber reinforcement results in stronger and more robust tools.
Tensile Strength | 590 MPa |
Tensile Modulus | 21 GPa |
Tensile Strain at Break | 3.80% |
Flexural Strength | 200 MPa |
Flexural Modulus | 22 GPa |
Flexural Strain at Break | 1.10% |
Compressive Strength | 180 MPa |
Compressive Modulus | 24 GPa |
Heat Deflection Temp | 105˚C |
Izod Impact - notched | 2600 J/m |
Density | 1.5 g/cm3 |
Price | TBD |
Lead Time | 2~3 days |
Wall Thickness | 1mm |
Tolerances | ±0.5mm |
Max part size | 330×270×200mm |
Layer height | 100 microns |
Disclaimer - Material properties are for general-purpose reference only and have been made available on a best effort basis for the users as a quick information guide for the material selection.
High Strength High Temperature (HSHT) glass fiber has high strength and retains strength in high temperatures environments. Not as stiff as carbon fiber but Onyx(strong nylon) parts reinforced with HSHT are strong in both low and high temperatures environments. Its strength is close to 6061-T6 Aluminum. HSHT reinforcement is best suited for parts in high-temperature environments like molds, autoclaves etc.
Tensile Strength | 600 MPa |
Tensile Modulus | 21 GPa |
Tensile Strain at Break | 3.90% |
Flexural Strength | 420 MPa |
Flexural Modulus | 21 GPa |
Flexural Strain at Break | 2.20% |
Compressive Strength | 216 MPa |
Compressive Modulus | 21 GPa |
Compressive Strain at Break | 0.80% |
Heat Deflection Temp | 150˚C |
Izod Impact - notched | 3100 J/m |
Density | 1.5 g/cm3 |
Price | TBD |
Lead Time | 2~3 days |
Wall Thickness | 1mm |
Tolerances | ±0.5mm |
Max part size | 330×270×200mm |
Layer height | 100 microns |
Disclaimer - Material properties are for general-purpose reference only and have been made available on a best effort basis for the users as a quick information guide for the material selection.
Kevlar based parts are known for their energy absorption and extreme toughness. When combined with Onyx(Strong Nylon) or another base material, it produces impact-resistant parts that are less prone to serious functional failure (fracture). Kevlar possesses excellent durability, making it optimal for parts that are subjected to repeated and sudden loading. As stiff as fiberglass and much more ductile, it can be used for a wide variety of applications.
Tensile Strength | 610 MPa |
Tensile Modulus | 27 GPa |
Tensile Strain at Break | 2.70% |
Flexural Strength | 240 MPa |
Flexural Modulus | 26 GPa |
Flexural Strain at Break | 2.10% |
Compressive Strength | 130 MPa |
Compressive Modulus | 25 GPa |
Compressive Strain at Break | 1.50% |
Heat Deflection Temp | 105˚C |
Izod Impact - notched | 2000 J/m |
Density | 1.2 g/cm3 |
Price | TBD |
Lead Time | 2~3 days |
Wall Thickness | 1mm |
Tolerances | ±0.5mm |
Max part size | 330×270×200mm |
Layer height | 100 microns |
Disclaimer - Material properties are for general-purpose reference only and have been made available on a best effort basis for the users as a quick information guide for the material selection.
Carbon Fiber Nylon - Generic Nylon combined with carbon fiber creates extremely high-strength material. Carbon fiber reinforcement increases the strength of generic nylon exponentially. It’s extremely stiff and strong and can be laid down in a wide variety of geometries.
ile Strength | 800 MPa |
Tensile Modulus | 60 GPa |
Tensile Strain at Break | 1.50% |
Flexural Strength | 540 MPa |
Flexural Modulus | 51 GPa |
Flexural Strain at Break | 1.20% |
Compressive Strength | 420 MPa |
Compressive Modulus | 62 GPa |
Compressive Strain at Break | 0.70% |
Heat Deflection Temp | 105˚C |
Izod Impact - notched | 960 J/m |
Density | 1.4 g/cm3 |
Price | TBD |
Lead Time | 2~3 days |
Wall Thickness | 1mm |
Tolerances | ±0.5mm |
Max part size | 330×270×200mm |
Layer height | 100 microns |
Disclaimer - Material properties are for general-purpose reference only and have been made available on a best effort basis for the users as a quick information guide for the material selection.
Glass Fiber Nylon - Generic Nylon combined with glass fiber creates very high-strength material. Glass fiber reinforcement increases the strength of generic nylon immensely. It’s extremely stiff and strong and can be laid down in a wide variety of geometries. Also, it's a more cost-effective option than carbon fiber.
Tensile Strength | 590 MPa |
Tensile Modulus | 21 GPa |
Tensile Strain at Break | 3.80% |
Flexural Strength | 200 MPa |
Flexural Modulus | 22 GPa |
Flexural Strain at Break | 1.10% |
Compressive Strength | 180 MPa |
Compressive Modulus | 24 GPa |
Heat Deflection Temp | 105˚C |
Izod Impact - notched | 2600 J/m |
Density | 1.5 g/cm3 |
Price | TBD |
Lead Time | 2~3 days |
Wall Thickness | 1mm |
Tolerances | ±0.5mm |
Max part size | 330×270×200mm |
Layer height | 100 microns |
Disclaimer - Material properties are for general-purpose reference only and have been made available on a best effort basis for the users as a quick information guide for the material selection.
Stainless Steel(17-4 PH) or SS630 is a multi-application material used for industrial uses. The density of 95% wrought strength. SS 17-4 PH enables you to make high-strength, robust metal parts for a wide variety of applications across the industrial spectrum.
Tensile modulus (Young Mod) | 140 GPa |
Tensile strength (UTM) | 1050 MPa |
Yield Strength | 800 MPa |
Elongation at break | 5% |
Hardness | 30 HRC |
Density | 96% |
Price | TBD |
Lead Time | 4~5 days |
Wall Thickness | 1mm |
Tolerances | ±0.5mm |
Max part size | 300×220×180mm |
Layer height | 125 microns |
Disclaimer - Material properties are for general-purpose reference only and have been made available on a best effort basis for the users as a quick information guide for the material selection.
Harder than 17-4 PH Stainless Steel and capable of maintaining material properties at high temperatures. TS H13 is an extremely versatile material to work with. Used for tool bodies, brazing fixtures, and other parts where hardness or heat resistance are required.
Tensile strength (UTM) | 1420 MPa |
Yield Strength | 800 MPa |
Elongation at break | 5% |
Hardness | 40 HRC |
Density | 94.50% |
Price | TBD |
Lead Time | 4~5 days |
Wall Thickness | 1mm |
Tolerances | ±0.5mm |
Max part size | 300×220×180mm |
Layer height | 125 microns |
Disclaimer - Material properties are for general-purpose reference only and have been made available on a best effort basis for the users as a quick information guide for the material selection.
Tool Steel A2 and D2 are cold work tool steels defined by their extremely high hardness after heat treatment. A2 tool steel offers a combination of good wear resistance and high toughness. D2 tool steel is harder and more wear-resistant, but less tough. Both can be used for cutting and forming tools, or other applications where high hardness are valued.
Tool Steel A2 | Tool Steel D2 | |
Tensile modulus (Young Mod) | 160 GPa | 187 GPa |
Compressive yield strength | 1170 MPa | 1690 MPa |
Hardness | 50 HRC | 55 HRC |
Density | 94.50% | 97.00% |
Price | TBD |
Lead Time | 4~5 days |
Wall Thickness | 1mm |
Tolerances | ±0.5mm |
Max part size | 300×220×180mm |
Layer height | 125 microns |
Disclaimer - Material properties are for general-purpose reference only and have been made available on a best effort basis for the users as a quick information guide for the material selection.
Inconel is a nickel-chromium-based superalloy that is extremely resistant to corrosion and strong at high temperatures. Can fabricate functional prototypes and end-use parts designed for harsh environments.
Inconel 625(FDM) | Inconel 625 | Inconel 718 | |
Tensile strength (UTM) | 765 MPa | 1000 MPa | 1241 MPa |
Yield Strength | 334 MPa | 680 MPa | 1034 MPa |
Elongation at break | 42% | 34% | 12% |
Hardness | 7 HRC | 27 HRC | 47 HRC |
Density | 96.50% | 98.00% | 98.00% |
Price | TBD |
Lead Time | 4~5 days |
Wall Thickness | 1mm |
Tolerances | ±0.5mm |
Max part size | 300×220×180mm |
Layer height | 100microns |
Disclaimer - Material properties are for general-purpose reference only and have been made available on a best-effort basis for the users as a quick information guide for the material selection.
Copper possesses better heat and electricity conductivity characteristics and can be formed into any geometrical shape. Application across a wide array of industries from electrical, electronics and automobile etc.
Tensile strength (UTM) | 193 Mpa |
Yield Strength | 26 MPa |
Elongation at break | 45% |
Thermal conductivity | 350 W/mK |
Electrical conductivity | 84% ICAS |
Density | 98.00% |
Price | TBD |
Lead Time | 4~5 days |
Wall Thickness | 1mm |
Tolerances | ±0.5mm |
Max part size | 300×220×180mm |
Layer height | 125 microns |
Disclaimer - Material properties are for general-purpose reference only and have been made available on a best effort basis for the users as a quick information guide for the material selection.
Figure 4® RUBBER-65A BLK material is created to address the needs for rubber parts featuring production-level performance and mechanical properties tested according to industry standards. Figure 4 RUBBER-65A BLK is a mid-tear strength, high elongation at break, Shore 65A material for the production of medium-hard rubber parts with the slow rebound
Price | TBD |
Lead Time | ~5 days |
Max part size | 124x70x196mm |
Disclaimer - Material properties are for general-purpose reference only and have been made available on a best effort basis for the users as a quick information guide for the material selection.
Stainless steel 316L is a corrosion-resistant iron-based alloy. Parts built from SS 316L can be machined, shot-peened and polished. Parts are not ideal in the temperature range 427°C - 816°C where precipitation of chromium carbides occurs. Due to the layer-wise building method, the parts have a certain anisotropy which could be seen from mechanical properties.
Price | TBD |
Lead Time | 3~4 days |
Wall Thickness | 1mm |
Tolerances | See below |
Max part size | 250×250×300mm |
Layer height | 100 microns |
Disclaimer - Material properties are for general-purpose reference only and have been made available on a best effort basis for the users as a quick information guide for the material selection.
Accura ClearVue's outstanding merger of clarity, material properties and processing speed makes it a high-performing and cost-effective option for aesthetic and functional prototypes used to improve product development efficiency of consumer goods, automotive, aerospace and medical components.
Price | TBD |
Lead Time | ~2 days |
Wall Thickness | 0.8mm |
Tolerances | ±0.1mm |
Max part size | 380x380x250mm |
Layer height | 100 microns |
Disclaimer - Material properties are for general-purpose reference only. They have been made available on a best-effort basis for the users as a quick information guide for the material selection.
Best for high-performance functional parts requiring high accuracy and mechanical strength. Biocompatible, with excellent surface quality and the ability to produce fine detail. Ideal applications include housings, enclosures, consumer-facing components, parts requiring textures or highly detailed design features.
Colour - Black
Properties |
Typical Values |
Viscosity, 30 °C |
210 MPa |
Viscosity, 50 °C |
80 MPa |
Density (printed part) |
1.2 g/cm³ |
Density (liquid resin) |
1.12 g/cm³ |
Tensile Properties |
Typical Values |
E Modulus |
2300 MPa |
Ultimate Tensile Strength |
60 MPa |
Elongation at Break |
25 % |
Flexural Properties |
Typical Values |
Flexural Modulus |
2400 MPa |
Flexural Strength |
110 MPa |
Impact Properties |
Typical Values |
Notched Izod (Machined), -30 °C |
20 J/m |
Notched Izod (Machined), 23 °C |
30 J/m |
Unnotched Izod, 23 °C |
509 J/m |
Charpy notched, 23 °C |
1.3 kJ/m² |
Thermal Properties |
Typical Values |
HDT at 0.45 MPa |
73 °C |
HDT at 1.82 MPa |
61 °C |
Flammability |
HB |
Glow-wire Test |
GWIT: 650°C GWFI: 625°C |
Hardness |
Typical Values |
Shore D |
80 |
Other |
Typical Values |
Biocompatibility |
ISO 10993 |
Price | TBD |
Lead Time | 4~5 days |
Wall Thickness | 0.8mm |
Tolerances | ±0.1mm |
Max part size | 192x108x370 mm |
Layer height | 100 microns |
Disclaimer - Material properties are for general-purpose reference only and have been made available on a best effort basis for the users as a quick information guide for the material selection.
Figure 4 HI TEMP 300-AMB is an ultra-high temperature plastic for applications requiring high heat resistance. It is the industry’s highest heat-resistant material with a heat deflection temperature of over 300 °C. This material is well suited for the testing of high-temperature components in applications including HVAC, consumer appliances, motor enclosures, stators, molds, and the like.
Tensile modulus (Young Mod) |
4000 MPa |
Tensile strength (UTM) |
81 MPa |
Elongation at break |
2.60% |
Flexural strength |
140 MPa |
Flexural modulus |
4260 MPa |
Hardness |
89D |
Heat deflection temp (Td) |
300˚C |
Density (Solid) |
1.3gm/cm3 |
Price |
TBD |
Lead Time |
2~3 days |
Wall Thickness |
1mm |
Tolerances |
±0.1mm |
Max part size |
- |
Layer height |
100 microns |
Disclaimer - Material properties are for general-purpose reference only and have been made available on a best-effort basis for the users as a quick information guide for the material selection.
STELLITE 6 is the most widely used of the wear-resistant cobalt-based alloys and exhibits good all-round performance. It is regarded as the industry standard for general-purpose wear-resistance applications, has excellent resistance to many forms of mechanical and chemical degradation over a wide temperature range, and retains a reasonable level of hardness up to 500°C (930°F). It also has good resistance to impact and cavitation erosion.
Tensile strength (UTM) | 850MPa |
Yield Strength | 700MPa |
Elongation at break | <1% |
Modulus of elasticity | 209MPa |
Hardnes | 36-45HRC |
Melting Temp. | 1250-1360˚C |
Thermal conductivity | 14.82 W/m.K |
Electrical resistivity | 106 μ-ohm.cm |
Density (Solid) | 8.44 g/cm³ |
Disclaimer - Material properties are for general-purpose reference only and have been made available on a best effort basis for the users as a quick information guide for material selection.
Aluminum 6061 is an extremely popular alloy, excellent for jobs that require forming or welding. It is the most commonly available aluminum alloy and provides a clean surface finish. Unlike other aluminum alloys, 6061 has high corrosion resistance. It can be forged, hot worked, and readily welded, as well as heat treated, annealed, and aged. It anodizes well and provides a bright, colourful finish.
Al 6061 | Al 6061-T6 (Hardened) | |
Temper | - | T6 |
Modulus of elasticity / Young Mod. | 68 GPa | 68 GPa |
Yield Strength | 55.2 MPa | 276 MPa |
Ultimate Tensile strength | 124 MPa | 310 MPa |
Elongation at break | 25% | 12 - 17% |
Hardness | 30 HRB | 60 HRB |
Max Working temp. | 130 - 150˚C | 130 - 150˚C |
Thermal expansion coefficient | 23.6 µm/m-°C | 23.6 µm/m-°C |
Thermal conductivity | 180 W/m-°C | 167 W/m-°C |
Electrical resistivity | 3.6 μΩ-cm | 3.9 μΩ-cm |
Corrosion | High Resistance | High Resistance |
Welding | High weldability | High weldability |
Price | TBD |
Lead Time | ~5 days |
Max part size | 500x500x500mm |
Disclaimer - Material properties are for general-purpose reference only and have been made available on a best effort basis for the users as a quick information guide for the material selection.
Aluminum alloy 7075 is the strongest of available aluminum alloys with zinc as a major element, excellent for jobs that require extreme strength while remaining lightweight. It possesses great cracking resistance and can be forged and heat-treated but is not ideal for welding. 7075 can be heat treated, annealed, and aged. It is not as ideal for anodizing compared to Aluminum 6061 and may produce a yellowish tint when clear anodizing.
Temper | T6 |
Modulus of elasticity / Young Mod. | 71 GPa |
Yield Strength | 503 MPa |
Ultimate Tensile strength | 572 MPa |
Elongation at break | 11% |
Hardness | 87 HRB |
Max Working temp. | 100˚C |
Thermal expansion coefficient | 23.6 µm/m-°C |
Thermal conductivity | 129 W/m-°C |
Electrical resistivity | 5.15 μΩ-cm |
Corrosion | Moderate Resistance |
Welding | Poor Weldability |
Price | TBD |
Lead Time | ~5 days |
Max part size | 500x500x500mm |
Disclaimer - Material properties are for general-purpose reference only and have been made available on a best effort basis for the users as a quick information guide for the material selection.
Aluminum alloy 2024 is an exceptionally high mechanical strength alloy, suitable for parts that require more strength while remaining lightweight. It also has excellent fatigue and cracking resistance, making it a desirable material for automotive & aircraft components. Aluminum 2024 can be machined to a high finish. It can be forged and hot worked but is not ideal for welding or soldering. 2024 responds well to heat treatment, annealing, and tempering. It can be anodized but results in a darker and less corrosion-resistant finish than Aluminum 6061.
Temper | T6 |
Modulus of elasticity / Young Mod. | 74 GPa |
Yield Strength | 345 MPa |
Ultimate Tensile strength | 427 MPa |
Elongation at break | 5% |
Hardness | 78 HRB |
Max Working temp. | 190˚C |
Thermal expansion coefficient | 23.2 µm/m-°C |
Thermal conductivity | 151 W/m-°C |
Electrical resistivity | 4.49 μΩ-cm |
Corrosion | Poor Resistance |
Welding | Good Weldability |
Price | TBD |
Lead Time | ~5 days |
Max part size | 500x500x500mm |
Disclaimer - Material properties are for general-purpose reference only and have been made available on a best effort basis for the users as a quick information guide for the material selection.
MIC6 Cast aluminum tooling plate offers superior dimensional stability and flatness compared to 6061 rolled plates. Being a cast product, it possesses very low internal stresses. Fully stress-relieved, Mic6 is a free-cutting aluminum alloy with excellent machining characteristics. Additionally, it is lightweight, smooth, and free from tension, contaminants, and porosity.
Modulus of elasticity / Young Mod. | 71 GPa |
Yield Strength | 105 MPa |
Ultimate Tensile strength | 165 MPa |
Elongation at break | 3% |
Hardness | 65 HB |
Max Working temp. | 400˚C |
Thermal expansion coefficient | 23.6 µm/m-°C |
Thermal conductivity | 142 W/m-°C |
Electrical resistivity | 4.79 μΩ-cm |
Corrosion | Good Resistance |
Welding | Good Weldability |
Price | TBD |
Lead Time | ~5 days |
Max part size | 500x500x500mm |
Disclaimer - Material properties are for general-purpose reference only and have been made available on a best effort basis for the users as a quick information guide for the material selection.
Copper alloy 110 is an extremely popular copper alloy, with a wide range of applications due to its high corrosion resistance, conductivity, and finish. It has the highest electrical conductivity of any metal, except silver. When exposed to the elements, it forms a thin protective patina that is relatively impermeable. Copper 110 is ideal when extensive machining is not required, as it has extremely low machinability compared to other copper alloys. It is excellent for hot and cold forming, as well as soldering. Copper 110 is not easily welded or brazed.
Temper | Annealed |
Modulus of elasticity / Young Mod. | 117 GPa |
Yield Strength | 283 - 345 MPa |
Ultimate Tensile strength | 296 - 359 Mpa |
Elongation at break | 3 - 16% |
Hardness | 57 HRB |
Thermal expansion coefficient | 17.6 µm/m-°C |
Thermal conductivity | 390 W/m-°C |
Electrical resistivity | 1.76 μΩ-cm |
Welding | Moderate Weldability |
Price | TBD |
Lead Time | ~5 days |
Max part size | 500x500x500mm |
Disclaimer - Material properties are for general-purpose reference only and have been made available on a best effort basis for the users as a quick information guide for the material selection.
Copper alloy C101 is the designation for moderate copper used in engineering applications. High ductility and impact strength also serve to make an extremely useful material. Copper alloy C101 is also known as HC or high conductivity copper and also has high thermal conductivity. Copper alloy C101 is, therefore, the material of choice for use in conductors and electrical components. It has a very high percentage of Copper in it - 99.9%.
Modulus of elasticity / Young Mod. | 115 GPa |
Yield Strength | 69 - 365 MPa |
Ultimate Tensile strength | 221 - 455 MPa |
Elongation at break | 55% |
Hardness | 75 - 90 HV |
Thermal expansion coefficient | 17 µm/m-°C |
Thermal conductivity | 383 - 391 W/m-°C |
Electrical resistivity | 1.74 μΩ-cm |
Corrosion | Good to excellent |
Welding | Poor Weldability |
Price | TBD |
Lead Time | ~5 days |
Max part size | 500x500x500mm |
Disclaimer - Material properties are for general-purpose reference only and have been made available on a best effort basis for the users as a quick information guide for the material selection.
Brass CDA 360 alloy has the highest machinability of all copper alloys, extremely popular for parts that require strength, weight, or a polished surface finish. Brass 360 has a very wide range of applications and is ideal for industrial and electronic industries. Unlike steel, 360 also forms a thin protective patina that does not rust. It has fair hot forming properties and is not ideal for cold forming, welding, soldering, and brazing. Brass 360 can be forged and annealed.
Modulus of elasticity / Young Mod. | 97 GPa |
Yield Strength | 124 - 310 MPa |
Ultimate Tensile strength | 338 - 469 MPa |
Elongation at break | 53% |
Hardnes | 63 HB |
Thermal expansion coefficent | 20.5 µm/m-°C |
Thermal conductivity | 115 W/m-°C |
Price | TBD |
Lead Time | ~5 days |
Max part size | 500x500x500mm |
Disclaimer - Material properties are for general-purpose reference only and have been made available on a best effort basis for the users as a quick information guide for the material selection.
AISI 1018 mild/low carbon steel has excellent weldability, produces a uniform and harder case, and is considered the best steel for carburized parts. AISI 1018 mild/low carbon steel offers a good balance of toughness, strength, and ductility. It produces exceptional welds that do not require pre- or post-heating processes. 1018 responds well to case hardening and heat treating.
Modulus of elasticity / Young Mod. | 200 GPa |
Yield Strength | 370 MPa |
Ultimate Tensile strength | 440 MPa |
Elongation at break | 15% |
Hardness | 71 HRB |
Thermal expansion coefficient | 12.1 µm/m-°C |
Thermal conductivity | 51.9 W/m-°C |
Electrical resistivity | 15.9 μΩ-cm |
Corrosion | Poor Resistance |
Welding | High weldability |
Price | TBD |
Lead Time | ~5 days |
Max part size | 500x500x500mm |
Disclaimer - Material properties are for general-purpose reference only and have been made available on a best effort basis for the users as a quick information guide for the material selection.
Steel alloy 1045 is a versatile medium carbon alloy, ideal for parts that require strength and impact resistance. Due to its higher carbon content, it has higher tensile strength. 1045 has excellent ductility and toughness. It is not ideal for welding or forming due to its higher carbon content. 1045 responds to heat treatment extremely well, but it is not ideal for case hardening.
Modulus of elasticity / Young Mod. | 206 GPa |
Yield Strength | 330 - 580 MPa |
Ultimate Tensile strength | 606 - 682 MPa |
Elongation at break | 13 - 18% |
Hardness | 89 HRB |
Thermal expansion coefficient | 12.1 µm/m-°C |
Thermal conductivity | 51.9 W/m-°C |
Electrical resistivity | 16 - 19 μΩ-cm |
Corrosion | Poor Resistance |
Welding | Good Weldability |
Price | TBD |
Lead Time | ~5 days |
Max part size | 500x500x500mm |
Disclaimer - Material properties are for general-purpose reference only and have been made available on a best effort basis for the users as a quick information guide for the material selection.
Steel alloy 4140 cold roll is a popular general-purpose alloy, ideal for parts that require high tensile strength and toughness. It has considerable atmospheric corrosion and wear resistance, and will not become brittle. It is not ideal for welding due to its lead content. It is often used for forging, responds very well to heat treatment, and can be annealed.
Modulus of elasticity / Young Mod. | 206 GPa |
Yield Strength | 660 - 965 MPa |
Ultimate Tensile strength | 896 - 1103 MPa |
Elongation at break | 17 - 22% |
Hardnes | 97 HRB |
Thermal expansion coefficent | 12.1 µm/m-°C |
Thermal conductivity | 42 W/m-°C |
Electrical resistivity | 22 μΩ-cm |
Corrosion | Good Resistance |
Welding | Moderate Weldability |
Price | TBD |
Lead Time | ~5 days |
Max part size | 500x500x500mm |
Disclaimer - Material properties are for general-purpose reference only and have been made available on a best effort basis for the users as a quick information guide for the material selection.
Steel alloy 1215 is a popular free-machining alloy (FMA), ideal for parts that require considerable machining and a bright finish. It responds well to slight bending, threading, and nibbling, but is not ideal for parts that may be subject to very severe fatigue stress. It possesses better weldability and formability and can be heat treated.
Modulus of elasticity / Young Mod. | 200 GPa |
Yield Strength | 415 MPa |
Ultimate Tensile strength | 540 MPa |
Elongation at break | 10% |
Hardnes | 85 HRB |
Thermal expansion coefficent | 11.5 µm/m-°C |
Thermal conductivity | 51.9 W/m-°C |
Electrical resistivity | 17.4 μΩ-cm |
Corrosion | Good Resistance |
Welding | Good Weldability |
Price | TBD |
Lead Time | ~5 days |
Max part size | 500x500x500mm |
Disclaimer - Material properties are for general-purpose reference only and have been made available on a best effort basis for the users as a quick information guide for the material selection.
ABS(Acrylonitrile Butadiene Styrene) blocks can be processed with ease and versatility. They can be machined, turned, drilled, milled, sawed, bored, die-cut, routed, and sheared using high-speed cutting tools. ABS can be machine finished by filing, grinding, sanding, buffing, and polishing.
Color - Natural, black
Modulus of elasticity / Young Mod. | 1.83 - 2.21 Gpa |
Yield Strength | 31.0 - 42.7 MPa |
Ultimate Tensile strength | 15.9 - 39.9 MPa |
Elongation at break | 10 - 50% |
Flexural Strength | 34.5 - 77.9 |
Hardness | 80.0 - 105 HRR |
Max Working temp. | Upto 70˚C |
Thermal expansion coefficient | 59.4 - 101 µm/m-°C |
Price | TBD |
Lead Time | ~5 days |
Max part size | 500x500x500mm |
Disclaimer - Material properties are for general-purpose reference only and have been made available on a best effort basis for the users as a quick information guide for the material selection.
Delrin (POM-H) is a versatile low-cost plastic in the acetal family, ideal for parts that require strength and resilience while machining to very tight tolerances. It has excellent dimensional stability and friction resistance, making it long-wearing. Unlike nylon, it has a very low moisture absorption rate, making it suitable for use in wet environments.
Color - Black & white
Modulus of elasticity / Young Mod. | 3.1 GPa |
Ultimate Tensile strength | 75 MPa |
Elongation at break | 30% |
Flexural Strength | 89 MPa |
Compressive Strength | 103 MPa |
Hardness | 122 HRR |
Max Working temp. | Upto 80˚C |
Thermal expansion coefficient | 84 µm/m-°C |
Thermal conductivity | 0.360 W/m-˚C |
UV Resistance | Moderate |
Price | TBD |
Lead Time | ~5 days |
Max part size | 500x500x500mm |
Disclaimer - Material properties are for general-purpose reference only and have been made available on a best effort basis for the users as a quick information guide for the material selection.
Nylon is a versatile low-cost plastic, ideal for parts that require high compressive strength and friction resistance while machining to very tight tolerances. It can be used in place of metal in some applications, allowing for longer-wearing parts that require lower maintenance than its metal counterpart. Nylon generally is stronger, withstands higher temperatures.
Color - Black, white
Modulus of elasticity / Young Mod. | 2.76 GPa |
Ultimate Tensile strength | 82 MPa |
Elongation at break | 30% |
Flexural Strength | 110 MPa |
Compressive Strength | 103 MPa |
Hardnes | 115 HRR |
Max Working temp. | Upto 90˚C |
Thermal expansion coefficent | 90 µm/m-°C |
Thermal conductivity | 0.24 W/m-˚C |
UV Resistance | Moderate |
Price | TBD |
Lead Time | ~5 days |
Max part size | 500x500x500mm |
Disclaimer - Material properties are for general-purpose reference only and have been made available on a best effort basis for the users as a quick information guide for the material selection.
Acrylic(PMMA) has excellent weathering resistance, especially applied to outdoor, ranking the highest in other plastics, and both a good surface hardness and gloss, processing plasticity, can be made of the required shape and products. Has extremely superior optical performance. Excellent transparency, light transmission rate of 92%, and can also be safe to use outdoor.
Color - Transparent
Modulus of elasticity / Young Mod. | 3.3 GPa |
Yield Strength | 72 MPa |
Ultimate Tensile strength | 35 MPa |
Elongation at break | 5% |
Flexural Strength | 105 MPa |
Compressive Strength | 103 MPa |
Hardnes | 80 - 100 HRM |
Max Working temp. | Upto 70˚C |
Thermal expansion coefficent | 70 µm/m-°C |
Thermal conductivity | 0.19 W/m-˚C |
UV Resistance | Good |
Price | TBD |
Lead Time | ~5 days |
Max part size | 500x500x500mm |
Disclaimer - Material properties are for general-purpose reference only and have been made available on a best effort basis for the users as a quick information guide for the material selection.
Polyether ether ketone (PEEK) is a popular high-strength plastic resin, ideal for parts that require strength and stiffness. It has an extremely high resistance to heat, moisture, and chemicals and can withstand multiple cycles in hot water or steam. PEEK also performs well in ultra-high vacuum environments.
Color - Black
Modulus of elasticity / Young Mod. | 4.3 GPa |
Ultimate Tensile strength | 110 MPa |
Elongation at break | 40% |
Flexural Strength | 172 MPa |
Compressive Strength | 138 MPa |
Hardness | 126 HRR |
Max Working temp. | Upto 240˚C |
Thermal expansion coefficient | 46.8 µm/m-°C |
Thermal conductivity | 0.25 W/m-˚C |
UV Resistance | Good |
Price | TBD |
Lead Time | ~5 days |
Max part size | 500x500x500mm |
Disclaimer - Material properties are for general-purpose reference only and have been made available on a best effort basis for the users as a quick information guide for the material selection.
PTFE (Polytetrafluoroethylene) commonly known as Teflon is an extremely resilient plastic, ideal for screw machine parts that require high-impact strength and durability. It has excellent resistance to frictional wear, weathering, flame, heat, chemicals, and radiation. Teflon is not affected by the ultraviolet and is resistant to oxidation, discolouration, and embrittlement. Teflon is completely resistant to hydrolysis. Teflon is a good barrier for water permeation.
Color - Black
Modulus of elasticity / Young Mod. | 0.4 - 0.5 GPa |
Yield Strength | 19 MPa |
Ultimate Tensile strength | 20 - 34 MPa |
Elongation at break | 2 - 4% |
Hardnes | 5.9 - 6.5 HV |
Max Working temp. | Upto 260˚C |
Price | TBD |
Lead Time | ~5 days |
Max part size | 500x500x500mm |
Polycarbonate is a transparent thermoplastic material with good strength and stiffness and outstanding impact resistance. It provides the best mechanical property and electrical insulation, high dimensional stability and excellent creep resistance. Polycarbonate's toughness and optical clarity make it ideal for a wide variety of applications. And it can be used in temperatures up to +110°C.
Color - Black, White, Semi-transparent
Modulus of elasticity / Young Mod. | 2 GPa |
Yield Strength | 60 - 70 MPa |
Ultimate Tensile strength | 61 MPa |
Elongation at break | 50 - 120% |
Flexural Strength | 90 MPa |
Compressive Strength | 17.7 - 21.7 HV |
Hardnes | 77 HRM |
Max Working temp. | Upto 110˚C |
Thermal expansion coefficent | 68 µm/m-°C |
Thermal conductivity | 0.89 - 0.21 W/m-˚C |
UV Resistance | Moderate |
Price | TBD |
Lead Time | ~5 days |
Max part size | 500x500x500mm |
Polypropylene (PP) is an economical material that offers a combination of outstanding physical, chemical, mechanical, thermal, and electrical properties not found in any other thermoplastic. Polypropylene has excellent chemical resistance in corrosive environments where there are organic solvents, degreasing agents, or electrolytic attacks, but poor resistance to aromatic, aliphatic, and chlorinated solvents. It is lightweight, non-staining, and exhibits a low moisture absorption rate. It’s ideal for the transfer of hot liquids and gases, and in vacuum system atmospheres with high heat and pressure.
Color - White
Modulus of elasticity / Young Mod. | 2 GPa |
Yield Strength | 60 - 70 MPa |
Ultimate Tensile strength | 61 MPa |
Elongation at break | 50 - 120% |
Flexural Strength | 90 MPa |
Compressive Strength | 17.7 - 21.7 HV |
Hardness | 77 HRM |
Max Working temp. | Upto 110˚C |
Thermal expansion coefficient | 68 µm/m-°C |
Thermal conductivity | 0.89 - 0.21 W/m-˚C |
UV Resistance | Moderate |
Price | TBD |
Lead Time | ~5 days |
Max part size | 500x500x500mm |
Disclaimer - Material properties are for general-purpose reference only and have been made available on a best effort basis for the users as a quick information guide for the material selection.
30% glass-filled nylon is suitable for use in the automotive industry & other general engineering applications where very high strength & resistance to high temperature is key. It also provides high strength and rigidity.
Price | TBD |
Lead Time | ~5 days |
Max part size | 400x400x500mm |
Disclaimer - Material properties are for general-purpose reference only and have been made available on a best effort basis for the users as a quick information guide for the material selection.
Stainless steel 316 is the standard molybdenum-bearing grade, second in importance to 304 amongst the austenitic stainless steels. The molybdenum gives 316 better overall corrosion-resistant properties than Grade 304, notably higher resistance to pitting and crevice corrosion in chloride environments. 316L stainless steel offers higher creep, stress to rupture and tensile strength at elevated temperatures.
Modulus of elasticity / Young Mod. | 193 GPa |
Yield Strength | 170 MPa |
Ultimate Tensile strength | 485 MPa |
Elongation at break | 40% |
Hardness | 95 HRB |
Thermal expansion coefficient | 15.9 µm/m-°C |
Thermal conductivity | 16.3 W/m-°C |
Electrical resistivity | 74 μΩ-cm |
Corrosion | High Resistance |
Welding | Excellent weldability |
Price | TBD |
Lead Time | 4~5 days |
Max part size | 500x500x500mm |
Disclaimer - Material properties are for general-purpose reference only and have been made available on a best-effort basis for the users as a quick information guide for the material selection.
SS 304 is the most versatile and widely used stainless steel available. And, is machinable and has good welding characteristics. It is non-magnetic and less thermally & electrically conductive. SS 304 can be readily braked or roll-formed into a variety of components for applications in the industrial, architectural, and transportation fields. Post-weld annealing is not required when welding thin sections. SS 304L is the low-carbon version of SS 304.
Modulus of elasticity / Young Mod. | 195 GPa |
Yield Strength | 240 MPa |
Ultimate Tensile strength | 585 MPa |
Elongation at break | 50% |
Hardness | 80 HRB |
Max Working temp. | 925˚C |
Thermal expansion coefficient | 17.3 µm/m-°C |
Thermal conductivity | 15.2 W/m-°C |
Electrical resistivity | 72 μΩ-cm |
Price | TBD |
Lead Time | 4~5 days |
Max part size | 500x500x500mm |
Disclaimer - Material properties are for general-purpose reference only and have been made available on a best effort basis for the users as a quick information guide for the material selection.
SS 17-4PH is also known as Grade360. It is precipitation-hardened steel with an unmatched union of excellent corrosion resistance, high strength and good mechanical characteristics. Its multi-properties provide designers with a unique opportunity to create reliable products with simplified manufacturing resulting in lower production costs. Not suitable for anodizing.
Yield Strength | 1000 MPa |
Ultimate Tensile strength | 1103 MPa |
Elongation at break | 5% |
Hardness | 35RC |
Max Working temp. | upto 316˚C |
Thermal expansion coefficient | 10.8 µm/m-°C |
Thermal conductivity | 17.3 - 18.7 W/m-°C |
Electrical resistivity | 98 μΩ-cm |
Corrosion | Excellent |
Welding | Good |
Price | TBD |
Lead Time | 4~5 days |
Max part size | 500x500x500mm |
Disclaimer - Material properties are for general-purpose reference only and have been made available on a best effort basis for the users as a quick information guide for the material selection.
ABS injection molding plastic is ideal for structural applications that require impact resistance, strength, and stiffness. It has excellent dimensional stability and is easy to paint and glue, making it the common choice. As a thermoplastic, ABS plastic can also be easily recycled.
Color - Black, white
Modulus of elasticity / Young Mod. | 1.35 - 2.35 GPa |
Yield Strength | 30 - 55 MPa |
Ultimate Tensile strength | 30 - 57 MPa |
Elongation at break | 10 - 70 % |
Flexural Strength | 47 - 92 MPa |
Hardnes | 78 - 116 HRR |
Max Working temp. | upto 70˚C |
Thermal expansion coefficent | 80 - 121 µm/m-°C |
Thermal conductivity | 0.170 W/m-˚C |
UV Resistance | Poor |
Price | TBD |
Lead Time | 2~3 weeks |
Max part size | 300x300x300mm |
Disclaimer - Material properties are for general-purpose reference only and have been made available on a best effort basis for the users as a quick information guide for the material selection.
Polypropylene (PP) is an economical material that offers a combination of outstanding physical, chemical, mechanical, thermal, and electrical properties not found in any other thermoplastic. Polypropylene has excellent chemical resistance in corrosive environments where there are organic solvents, degreasing agents, or electrolytic attacks, but poor resistance to aromatic, aliphatic, and chlorinated solvents. It is lightweight, non-staining, and exhibits a low moisture absorption rate. It’s ideal for the transfer of hot liquids and gases, and in vacuum system atmospheres with high heat and pressure.
Color - Black, white
Modulus of elasticity / Young Mod. | 1.31 GPa |
Yield Strength | 31 MPa |
Ultimate Tensile strength | 33 MPa |
Elongation at break | 400% |
Flexural Strength | 33 MPa |
Compressive Strength | 34 MPa |
Hardness | 78 Shore D |
Max Working temp. | upto 80˚C |
Thermal expansion coefficient | 114 µm/m-°C |
UV Resistance | Poor |
Price | TBD |
Lead Time | 2~3 weeks |
Max part size | 300x300x300mm |
Disclaimer - Material properties are for general-purpose reference only and have been made available on a best effort basis for the users as a quick information guide for the material selection.
Polycarbonate is a transparent thermoplastic material with good strength and stiffness and outstanding impact resistance. It provides the best mechanical property and electrical insulation, high dimensional stability, and excellent creep resistance. Polycarbonate's toughness and optical clarity make it ideal for a wide variety of applications. And it can be used in temperatures up to +110°C.
Color - Black, transparent
Modulus of elasticity / Young Mod. | 3.7 GPa |
Yield Strength | 62 MPa |
Ultimate Tensile strength | 64 MPa |
Elongation at break | 90% |
Flexural Strength | 91 MPa |
Compressive Strength | 82 MPa |
Hardness | 122 HRR |
Max Working temp. | upto 110˚C |
Thermal expansion coefficient | 68 µm/m-°C |
Thermal conductivity | 0.19 W/m-˚C |
UV Resistance | Poor |
Price | TBD |
Lead Time | 2~3 weeks |
Max part size | 300x300x300mm |
Disclaimer - Material properties are for general-purpose reference only and have been made available on a best effort basis for the users as a quick information guide for the material selection.
Nylon has excellent strength, stiffness, heat resistance, wear-resistance and lubricity, chemical resistance to hydrocarbon. Nylon is a relatively low cost to performance of engineering-grade polymers. Nylon is easy to process and can be reinforced with glass or carbon fiber to increase mechanical and thermal properties.
Glass-filled nylon is mostly used in applications that require properties such as high rigidity, high degree of hardness, high creep strength, high dimensional stability, good fatigue resistance, and high mechanical strength.
Color - Black
Properties | Nylon PA6 | Nylon PA6 GF10 | Nylon PA6 GF20 |
Modulus of elasticity / Young Mod. | 3.7 GPa | 4.7 GPa | 5.13 GPa |
Yield Strength | 63 MPa | 103 MPa | 115 MPa |
Ultimate Tensile strength | 82 MPa | 92 MPa | 101 MPa |
Elongation at break | 30% | 5% | 5.4% |
Flexural Strength | 110 MPa | 140 MPa | 155 MPa |
Compressive Strength | 103 MPa | - | 117 MPa |
Hardness | 115 HRR | 119 HRR | 90 - 122 HRR |
Max Working temp. | upto 90˚C | upto 100˚C | upto 130˚C |
Thermal expansion coefficient | 90 µm/m-°C | 45 µm/m-°C | 34 µm/m-°C |
Thermal conductivity | 0.245 W/m-˚C | 0.303 W/m-˚C | 0.345 W/m-˚C |
UV Resistance | Moderate | Moderate | Moderate |
Price | TBD |
Lead Time | 2~3 weeks |
Max part size | 300x300x300mm |
Disclaimer - Material properties are for general-purpose reference only and have been made available on a best effort basis for the users as a quick information guide for the material selection.
Polyoxymethylene (POM) or Delrin injection molding material, often referred to as Delrin or acetal is an engineered thermoplastic material that is used to manufacture parts that require increased stiffness, low friction versatility, and greater dimensional stability.
Color - Black, white
Modulus of elasticity / Young Mod. | 2.76 GPa |
Ultimate Tensile strength | 61 MPa |
Elongation at break | 30% |
Flexural Strength | 82 MPa |
Compressive Strength | 93 MPa |
Hardness | 120 HRR |
Max Working temp. | upto 80˚C |
Thermal expansion coefficient | 92 µm/m-°C |
Thermal conductivity | 0.231 W/m-˚C |
UV Resistance | Moderate |
Price | TBD |
Lead Time | 2~3 weeks |
Max part size | 300x300x300mm |
Disclaimer - Material properties are for general-purpose reference only and have been made available on a best effort basis for the users as a quick information guide for the material selection.
PC-ABS combines the strength and heat resistance of polycarbonate with the flexibility of ABS. Increased toughness and dimensional stability, higher heat resistance than ABS, and improved low-temperature impact resistance than PC. It is frequently used when increased mechanical properties are required when using ABS or when a lower-cost PC is required. The material can be modified by the addition of glass fiber, mineral fillers, and flame retardant.
Color - Black, white
Modulus of elasticity / Young Mod. | 2.4 GPa |
Ultimate Tensile strength | 54 MPa |
Elongation at break | 30% |
Flexural Strength | 90 MPa |
Max Working temp. | upto 110˚C |
Thermal expansion coefficient | 81 µm/m-°C |
Price | TBD |
Lead Time | 2~3 weeks |
Max part size | 300x300x300mm |
Disclaimer - Material properties are for general-purpose reference only and have been made available on a best effort basis for the users as a quick information guide for the material selection.
PMMA has excellent weathering resistance, especially applied to outdoor, ranking the highest in other plastics, and both a good surface hardness and gloss, processing plasticity, can be made of the required shape and products. Has extremely superior optical performance. Excellent transparency, light transmission rate of 92%, and can also be safe to use in outdoor.
Color - Transparent
Yield Strength | 60 MPa |
Ultimate Tensile strength | 64 MPa |
Elongation at break | 10% |
Flexural Strength | 103 Mpa |
Compressive Strength | 102 Mpa |
Hardness | 69 HRR |
Max Working temp. | upto 70˚C |
Thermal expansion coefficient | 70 µm/m-°C |
Thermal conductivity | 0.199 W/m-˚C |
UV Resistance | Good |
Price | TBD |
Lead Time | 2~3 weeks |
Max part size | 300x300x300mm |
Disclaimer - Material properties are for general-purpose reference only and have been made available on a best effort basis for the users as a quick information guide for the material selection.
EPDM(Ethylene Propylene Diene Monomer) rubber is a low-cost option for parts having outdoor applications, exposure to moisture and electrical insulations, and, has good tear resistance. EPDM exhibits good resistance when exposed to ozone, UV rays, ageing and steam environments. However, EPDM is unsuitable for food applications and vulnerable to hydrocarbon oils, solvents, and some lubricating oils. Also, EPDM is not flame resistant.
Price | TBD |
Lead Time | 2~3 weeks |
Max part size | 300x300x300mm |
Disclaimer - Material properties are for general-purpose reference only and have been made available on a best effort basis for the users as a quick information guide for the material selection.
NBR (nitrile-butadiene rubber) is tough and resistant to varying temperatures. The percentage of acrylonitrile decides its oil resistance property. More acrylonitrile means more resistance to oil swelling and gases, and, makes it stronger. Less acrylonitrile means more flexibility at lower temperatures. NBR is not suitable for some chemicals, outdoor applications, and sunlight and has lower flame resistance.
Price | TBD |
Lead Time | 2~3 weeks |
Max part size | 300x300x300mm |
Disclaimer - Material properties are for general-purpose reference only and have been made available on a best effort basis for the users as a quick information guide for the material selection.
It is closed cell flexible foam created to provide flexible & soft insulation material. It has an excellent performance in hot and cold temperature environments. It has excellent moisture resistance capability saving the enclosed metal parts from corrosion and has some flame retardant characteristics.
Price | TBD |
Lead Time | 2~3 weeks |
Max part size | 300x300x300mm |
Disclaimer - Material properties are for general-purpose reference only and have been made available on a best effort basis for the users as a quick information guide for the material selection.
PVC greatly enhances ozone, thermal ageing, and chemical resistance of NBR in various industrial applications. PVC also vastly improves abrasion resistance, tear resistance, and tensile properties. It also adds gloss and improves the finish of the extruded stock and imparts flame-retardant character. NBR/PVC blends can be conveniently milled, extruded, and compression-molded
Price | TBD |
Lead Time | 2~3 weeks |
Max part size | 300x300x300mm |
Disclaimer - Material properties are for general-purpose reference only and have been made available on a best effort basis for the users as a quick information guide for the material selection.
AISI 1018 mild/low carbon steel has excellent weldability, produces a uniform and harder case and it is considered the best steel for carburized parts. AISI 1018 mild/low carbon steel offers a good balance of toughness, strength, and ductility. It produces exceptional welds that do not require pre- or post-heating processes. 1018 responds well to case hardening and heat treating.
Modulus of elasticity / Young Mod. | 200 GPa |
Yield Strength | 370 MPa |
Ultimate Tensile strength | 440 MPa |
Elongation at break | 15% |
Hardness | 71 HRB |
Thermal expansion coefficient | 12.1 µm/m-°C |
Thermal conductivity | 51.9 W/m-°C |
Electrical resistivity | 15.9 μΩ-cm |
Corrosion | Poor Resistance |
Welding | High weldability |
Price | TBD |
Lead Time | 2~3 weeks |
Max part size | 200x200x200mm |
Disclaimer - Material properties are for general-purpose reference only and have been made available on a best effort basis for the users as a quick information guide for the material selection.
Stainless steel 304 It is the most versatile and most widely used stainless steel available and has excellent forming and welding characteristics. SS 304 can be readily braked or roll-formed into a variety of components for applications in the industrial, architectural, and transportation fields. Post-weld annealing is not required when welding thin sections.
Modulus of elasticity / Young Mod. | 195 GPa |
Yield Strength | 240 MPa |
Ultimate Tensile strength | 585 MPa |
Elongation at break | 50% |
Hardness | 80 HRB |
Max Working temp. | 925˚C |
Thermal expansion coefficient | 17.3 µm/m-°C |
Thermal conductivity | 15.2 W/m-°C |
Electrical resistivity | 72 μΩ-cm |
Price | TBD |
Lead Time | 2~3 weeks |
Max part size | 300x300x300mm |
Disclaimer - Material properties are for general-purpose reference only and have been made available on a best effort basis for the users as a quick information guide for the material selection.
Stainless steel 316 is the standard molybdenum-bearing grade, second in importance to 304 amongst the austenitic stainless steels. The molybdenum gives 316 better overall corrosion resistant properties than Grade 304, particularly higher resistance to pitting and crevice corrosion in chloride environments. 316L stainless steel offers higher creep, stress to rupture, and tensile strength at elevated temperatures.
Modulus of elasticity / Young Mod. | 193 GPa |
Yield Strength | 170 MPa |
Ultimate Tensile strength | 485 MPa |
Elongation at break | 40% |
Hardness | 95 HRB |
Thermal expansion coefficient | 15.9 µm/m-°C |
Thermal conductivity | 16.3 W/m-°C |
Electrical resistivity | 74 μΩ-cm |
Corrosion | High Resistance |
Welding | Excellent weldability |
Price | TBD |
Lead Time | 2~3 weeks |
Max part size | 200x200x200mm |
Disclaimer - Material properties are for general-purpose reference only and have been made available on a best effort basis for the users as a quick information guide for the material selection.
ABS type thermoplastic where temperature resistance is required. Good chemical resistance. Good impact and flexural resistance.
ABS (PX223) Temperature resistance up to 110°C.
ABS High temp (PR700) Temperature resistance up to 130°C.
Color - Black
Grade | ABS (PX223) | ABS HT (PR700) |
Modulus of elasticity / Young Mod. | 2.3 GPa | 1.8 GPa |
Ultimate Tensile strength | 60 MPa | 60 MPa |
Elongation at break | 11% | 13% |
Flexural Strength | 80 MPa | 80 MPa |
Impact strength | > 60 KJ/m2 | > 60 KJ/m2 |
Hardness | 80 Shore D | 82 Shore D1 |
Heat Deflection Temp. (HDT) | 110˚C | 130˚C |
Glass Transition Temp. (TG) | >120˚C | >130˚C |
Price | TBD |
Lead Time | 4~5Days |
Max part size | 500x500x500mm |
Semi-rigid PP/HDPE-like for any need for the semi-flexible part with high impact resistance and mechanically demanding applications. Temperature resistance upto 90°C.
Color - Light brown
Grade | PR777 |
Modulus of elasticity / Young Mod. | 1 GPa |
Ultimate Tensile strength | 32 MPa |
Elongation at break | 35% |
Flexural Strength | 35 MPa |
Impact strength | > 60 KJ/m2 |
Hardness | 75 Shore D1 |
Heat Deflection Temp. (HDT) | 90˚C |
Glass Transition Temp. (TG) | >120˚C |
Price | TBD |
Lead Time | 4~5Days |
Max part size | 500x500x500mm |
Nylon (VC3360) is a polyurethane vacuum casting resin designed to simulate thermoplastics such as Nylon and glass-filled Nylon. It has a high flexural modulus, excellent physical properties.
Color - Light brown
Ultimate Tensile strength | 80 - 85 MPa |
Elongation at break | 10 - 12% |
Hardness | 85 - 90 Shore D |
Heat Deflection Temp. (HDT) | - |
Glass Transition Temp. (TG) | 82 - 87˚C |
Price | TBD |
Lead Time | 4~5Days |
Max part size | 500x500x500mm |
Polycarbonate is suitable for optical piece prototyping. Very high UV stability. Easy to polish and to color.
Polycarbonate PRC1710. Temperature resistance upto 93°C.
Polycarbonate high temp PRC1708. Temperature resistance upto 105°C.
Color - Transparent
Grade | PC (PRC1710) | PC HT (PRC1708) |
Color | Transparent | Transparent |
Modulus of elasticity / Young Mod. | 2.4 GPa | 2.3 GPa |
Ultimate Tensile strength | 65 MPa | 70 MPa |
Elongation at break | 15% | 16% |
Flexural Strength | 84 MPa | 80 MPa |
Impact strength | 48 KJ/m2 | 90 KJ/m2 |
Hardness | 87 Shore D1 | 87 Shore D1 |
Heat Deflection Temp. (HDT) | 93˚C | 105˚C |
Glass Transition Temp. (TG) | 100˚C | 110˚C |
Price | TBD |
Lead Time | 4~5Days |
Max part size | 500x500x500mm |
EPDM VC 3300 is a flexible, polyurethane material. By altering the ratio of the formulation, the hardness of the cured rubber can be selected. Very soft elastomers of 35 (Shore A) through tough, semi-flexible elastomers of 95 (Shore A) can be achieved.
Color - Black
EPDM 3300 (Black Color) | ||||||||
Properties | Unit | Result | ||||||
Hardness | Shore A | 35 | 45 | 55 | 65 | 75 | 85 | 95 |
Tensile Strength | MPa | 1.5 – 3.5 | 3.0 – 5.0 | 4.0 – 6.0 | 6.0 – 8.0 | 7.5 – 9.5 | 9.5 – 11.5 | 9.5 – 11.5 |
Elongation at Break |
% | 900 – 1100 | 1100 – 1300 | 700 – 800 | 500 – 600 | 400 – 500 | 300 – 400 | 200 – 300 |
Tear Strength | KN/m | 7 - 11 | 13 - 17 | 17 - 23 | 22 - 28 | 36 - 42 | 55 - 61 | 74 - 80 |
Max Operating Temp. | ˚C | 60 | 60 | 60 | 60 | 80 | 80 | 80 |
Price | TBD |
Lead Time | 4~5Days |
Max part size | 500x500x500mm |