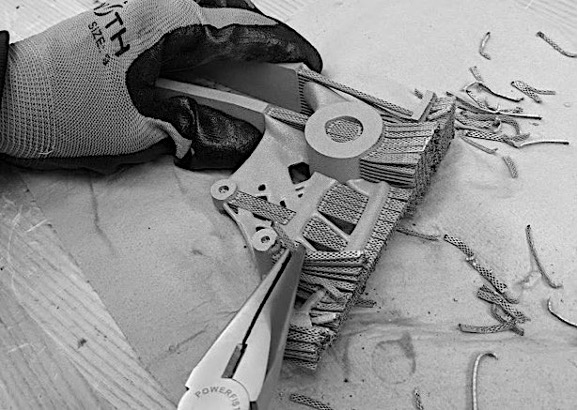
Overview
Metal AM part is created from CAD data made by the designer which is fed into the SLM machine which ultimately creates the physical part. Quality of build depends upon factors like design methodology, material quality, machine settings etc. Once the part is created, additional post-processing is required to bring it closer to the application needs. Post-processing is an important feature of any SLM process. Post-processing involves mandatory removal of residual stresses, removal of support structures, surface finishing, dimensional tolerances to meet application specifications.
Post-processing techniques
- Heat treatment
- Support removal
- Hot Isostatic Pressing(HIP)
- Machining
- Abrasive Blasting
- Micro finishing
- Polishing
- Laser Remelting
Heat treatment
During the SLM process, residual stresses are induced into the formed components. Hence, the first step is to remove those stress by heat treatment in a furnace. The components are placed inside the furnace and are allowed to creep till the stresses have eased followed by some degree of plastic deformation. After the heat treatment, the parts are separated in one go from the base plate typically by wire cut cutting process.
Metal parts inside the furnace for sintering. Photo credits: Markforged
Support removal
Supports are required to create angled surfaces or overhang features. Support structures are removed after the part is separated from the build plate. Support structures are removed by mechanical means since the structures are tightly welded onto the part. For smaller parts, pliers and small cutting tools are sufficient to clear the supports. For larger parts, CNC milling or turning is used to clear supports along with the surface finish to achieve tolerances according to the application. Supports structures are designed in such a way that later can be removed easily by creating breakpoints and space for tool insertion.
Support removing process. Photo credits: Novick
Hot Isostatic Pressing(HIP)
Hot Isostatic Pressing(HIP) improves the mechanical properties of the SLM parts by exposing them to temperatures slightly below their melting point under very high pressure. Under these conditions, fine pores and small cracks get filled. Due to very high pressure, diffusion occurs nearly removing all kinds of surface defects. This makes the part tough and strong to withstand high forces and stress during application.
HIP system. Photo credits: metal-am
Machining
SLM parts are normally machined to remove supports, improve surface finish and achieve tighter geometric tolerances according to the application requirements. The part obtained from the SLM process is near net shape then it is cut to get final dimensions. Conventional machining processes such as milling, turning, drilling, reaming, grinding is applied to achieve the desired shape. Fastener thru-holes, fitment or assembly dimensions, location pins/holes, tiny shapes which cannot be printed accurately are some of the features that require machining to bring it within design parameters.
CNC machining of SLM parts. Photo credits: Autodesk
Abrasive Blasting
Abrasive blasting is the most fundamental method of improving the surface finish of SLM parts. The abrasive material is blasted onto the surface by a high-pressure gas stream. If the abrasive material is metal or glass, then the process is known as shot peening. Shot peening improves the surface finish and increases parts fatigue life by introducing the compressive residual stresses at the surface.
Abrasive blasting. Photo credits: Protocast
Shot Peening. Photo credits: CWST
Micro finishing
Surface finishing could be further enhanced by micro polishing which uses a very fine abrasive material in the form of slurry. According to the surface geometry, abrasive material is introduced into the flow targeted to an area or fixed to the surface. Sinusoidal movement of the flow is then precisely manipulated according to the movement of the part so that the surface roughness is removed only on the specific targeted location of the part.
Micro finished turbine blade. Photo credits: Bel Air Finishing
Polishing
Additionally, the surface finish of SLM parts could also be improved by conventional polishing. Adequate polishing with fine abrasive material could readily achieve a mirror-like finish. For example, a mirror-like finish is applied on injection molding inserts made by SLM
Polishing of SLM parts. Photo credits: Moleroda
Laser remelting
Laser remelting is another process to improve the surface finish of SLM parts. This process is done after finishing the top layer of the part. The top surface is re-melted using a laser scan creating a shallow depth of melted material, levels evenly once the melt solidifies. This process is only applicable to top facing surfaces that are not in contact with the powder or could be applied to all surfaces after removing all unfused power.