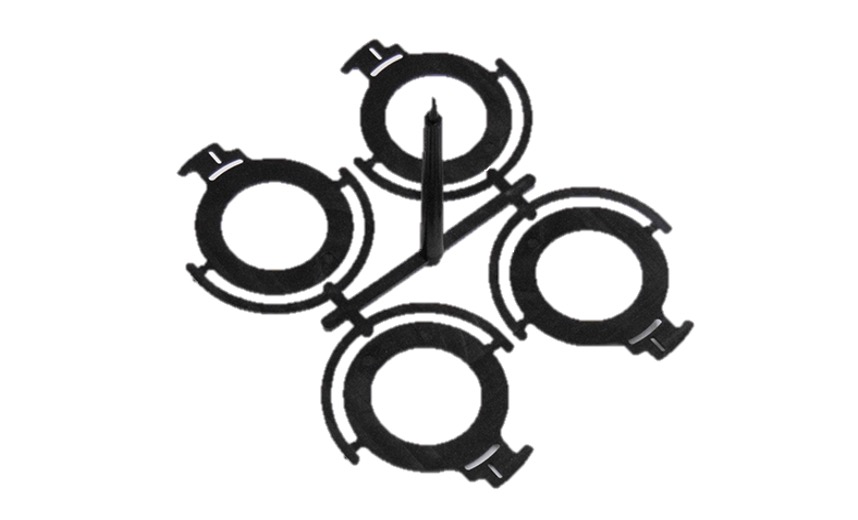
Overview
Post-processing of injection molded parts is very important since Injection molding forms plain plastic parts. Most of the time bare plastic parts are used as it is but sometimes due to the design of the component or some special requirement, injection molded parts are post-processed in many ways. Finishing options like painting, ultrasonic welding, and cubic printing are a few of the commonly available technologies. In the following article, we are going to explore in detail all major post-processing technologies.
IM Post-processing techniques
- Painting
- Pad printing
- Hot stamping
- Part assembly
- Laser engraving
- Ultrasonic welding
- Vibration welding
- Infrared welding
- Hot plate welding
- Hot air cold welding
- Heat staking
- Cubic printing
- Overmolding
Painting
Some applications needed specific colour tone, gloss etc which cannot be achieved during the injection molding process. Spray painting is the most common type of surface coating or surface finish and is cost-effective. Some paint processes are single step or multi-step procedures. Some paints needed UV curing to increase the durability of the paint if they are meant for outdoor application. Another process is powder coating in which powder is sprayed onto the surface and later UV cured. Silk screening is used to make colour patterns on the surface. A thin plastic sheet screen is prepared with pattern holes/cutouts are created on it. The holes/cut-out make sure that paint strikes the plastic surface wherever needed. The desired pattern emerges once the screen is removed from the plastic surface.
Photo credits: icomold
Pad printing
In this process, a large raised pad is made with the desired pattern. Then the paint is applied to the pad and stamped onto the plastic surface. Then the paint is cured or dried according to the paint specifications and injection molding process. This is one of the most cost-effective and simple process.
Pad Printing
Hot stamping
Hot stamping is generally used to apply a design or decorate raised shapes on the plastic part. The design or graphic is transferred onto the surface by pressing the patterned foil against the raised feature by the heated die. The die pressure along with heat transfers the colour or pigment from the foil to the plastic. The die shape is the same as that of the projected area. Hot stamping is used to imprint pictorial or text information, company logos, colour, texture etc. The die is made out of either steel, magnesium, copper, brass depending upon the kind of artwork needed and production volume.
Hot stamping
Part assembly
Many times a design consists assembly of many individual parts. In that case, each part is injection molded and later assembled either manually or robotically. A proper fixture is made to ensure correct assembly alignment and orientation. Manual assembly is generally suitable for simpler assemblies with fewer parts, however, for large assemblies machine assembly or robotic assembly is more suitable.
Laser engraving
The laser engraving process removes a portion of the plastic part surface by the laser beams. The removed plastics creates tiny cavities which appear like some printed texts. The targeted surface area gets vaporised instantly due to high heat generation when hit by the laser beams. Laser engraving is of three types based on the engraving requirements are etching, deep engraving, laser ablation. Laser engraving is one of the fastest and easiest ways of creating serial numbers and logos on the plastic part.
Laser engraving of symbols
Ultrasonic welding
In this process, parts are fused together by the heat generated due to friction. One part is kept stationary while the other part moves back and forth or up & down at very high-frequency generation heat due to friction. This process creates a simplified assembly of parts without any need for fasteners, adhesives etc. US welding machines are just like any other spot welding or resistance welding machine. US welding greatly simplifies the design of the product as well as the manufacturing process completely removing the need to any assembly fasteners, adhesive and assembly fixtures. US welding is most suitable for the designs when it cannot be molded in a single piece like enclosure, hermetically sealed containers etc.
Vibration welding
Vibration welding is the process of joining plastic parts by the heat generated due to friction under pressure at the mating edges due to liner horizontal motion between the parts. The heat generated melts the plastic edges creating a fusion. One part is kept stationary while the other moves in a linear direction. Vibration works at lower frequencies, with more clamping force and higher amplitude. Key advantages of vibration welding are taking less time to weld, energy efficiency and no visible marks.
Vibration welding
Infrared welding
Plastic parts are joined together by the heat generated from the infrared radiation source. The radiating from the source is absorbed by the plastic material and the exposed surface gets melted. The parts are joined by pressing them against each other. Heat transfer takes place without any physical contact between the heat source and target parts. This process is quick, has no contact, is precisely controlled, and particle free. 2D, 3D and other complex shapes can be easily welded into shapes for example car door trims, car air conditioning ducts, liquid tanks etc.
Hot plate welding
This process used a heated plate to melt the plastic part edges/surface to join. Once heated sufficiently, the heated plate is removed and the two parts are pressed together to create jointly. Precise controls are deployed to ensure the entire process right from the heating/melting to joint making is trouble-free. This process creates a strong, leak-proof hermetically sealed joint. Fixtures are made to ensure correct alignment and orientation. This process is generally used for semi-crystalline, softer thermoplastics like PP and PE. Chemically compatible dissimilar materials could also be used if their melts temperature and viscosities are in close range.
Hot air cold welding
This process melts the plastic surface/edges by the stream of hot air and joined together. In this process, a plastic substrate and a welding rod is used for creating a joint or filling. Hot air blowing from the gun is controlled along with the pressure applied on the welding rod to create a perfect joint. Since this is done manually, the quality of the weld entirely depends upon the skill of the welder. Applications are repair of car bumper cracks, plastic air flow ducts, chemical storage containers etc.
Hot air cold welding
Heat staking
This process is very similar to metal riveting, however, heat is used to form the plastic projection to create a joint or connection. This process is used for joining two dissimilar materials example assembly between plastic and metal. In this process, heating and cooling is being carried out successively locally to melt and reform the plastic shape. An application like joining a PCB to a plastic enclosure, joining plastic parts of an automobile etc. The advantage of this process is that there’s no residue, no particulate and no vibrations.
Photo credits: Emerson
Cubic printing
Cubic printing is the surface decoration technology where the designs are transferred onto the plastic surface from specially printed films. The special films are made to float on the water surface and then the plastic part is dipped slowly pressing against the special film capturing the design on the plastic surface. This technology can be applied to a diverse range of materials from 2D to 3D complex shapes from automobiles, home appliances, plastic furniture etc.
Photo credits: hgarts
Overmolding
Overmolding is the process in which plastic or rubber material is overmolded onto an already existing plastic or metal part. This is done to increase the external aesthetic value of the product to make it more appealing to the customers or rubber-like material to enhance grip. Enhancing product performance is the basic reason to fabricate products by overmolding. Overmolding also saves from the hassles of manually adding the part where the tolerance and performance are the key parameters. Examples are multicolour toothbrushes, hammer/handle grip, etc.
Overmolding