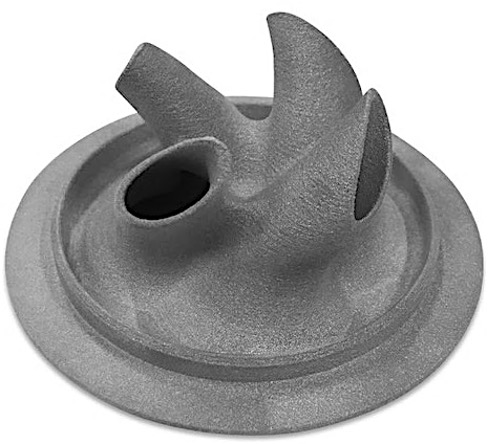
Selective laser sintering (SLS) is also known as the powder bed fusion process. SLS systems print thermoplastic polymer materials, polymer composites, or in some cases ceramics.
SLS processes begin by spreading a thin layer of powder across the build platform. Then cross-sections are melted layer by layer at a time, mostly using a laser beam, electron beam, or intense infrared lamps
Success with SLS starts with parts optimized for the printing process. The following guide captures the important design factors that are generally applied during designing parts for SLS.
Supported wall thickness
Supported walls are joined with other walls or shapes on at least two sides. The minimum vertical wall thickness of 0.6 mm. The minimum horizontal wall thickness of 0.3 mm
Unsupported wall thickness
A wall without support is one that is joined with other walls on less than two sides. The minimum vertical wall thickness of 0.6 mm. The minimum horizontal wall thickness of 0.3 mm
Minimum pin diameter
A minimum diameter of 0.8mm of the pin can be printed successfully.
Holes
The Minimum recommended hole diameter is 1.0 mm. Size below 1.0mm may not appear
Clearance for connecting or moving parts
0.5mm clearance for any mating and sliding parts
Embossing & engraving
Embossed details are small raised features on your design. Details smaller than 1mm in thickness and 1mm in height may not be visible on your print.
Engraving is the practice of incising a design onto a surface either flat or curved. The minimum recommended depth and width of 1mm should be maintained.
Powder escape holes
Make escape holes for the enclosed shells which remain filled with powder. Create at least 2 escape holes of a minimum diameter of ∅3.5mm
Tolerance
Industrial SLA printing has a dimensional tolerance of ± 0.3% of feature dimensions and a lower limit of ± 0.3 mm.