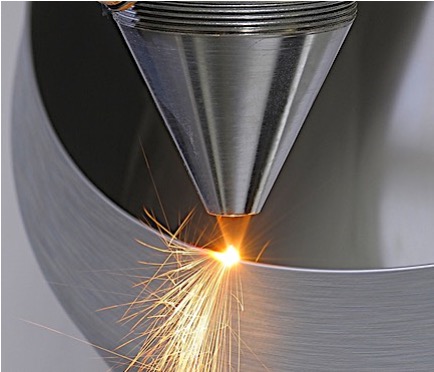
Additive manufacturing (AM), is an innovative way to industrial production also known as 3D printing. AM warrants the production of tougher, lightweight and complex designs. These complex shapes are difficult to create using conventional manufacturing technologies. AM can be used to make a tool that wouldn't make sense to fabricate conventionally due to its high cost. Here we’re going to discuss various applications which are affected by AM.
The key applications of AM are –
- Prototyping
- Tooling's
- Performance enhancement
- Part Production
- Custom parts
- Spare parts
- Architecture
Prototyping
For the past decades, prototyping was the only application of AM. Many of today's AM technologies were referred to as RPT or rapid prototyping. Prototyping is still the key driver of sales of most AM set-up
Types of prototyping –
Direct prototyping - AM is used to create a quick prototype part for analysis or proof of concept.
Indirect prototyping - AM is used to create the tool used to make the prototype using a conventional process.
The application of AM for prototyping can differ in major ways. Depending on the selected process and final application of the part. AM application for fast prototyping is an important stage in any product development process. It can increase confidence in the product manifolds and reduce risks.
Toolings
AM is searching for its place in the industry to improve the performance of conventionally made toolings. AM can be used to create prototype molds for short-run productions. AM can be used to create tools that assist in different operations, such as locating fixtures, jigs, and ergonomic supports. Some AM processes can be used to produce main tooling's, molds. Also, for cutting tools for high-production injection molding and machining.
AM made tooling can offer the following benefits:
Speed – AM-based tooling can be produced faster than conventional tooling. The specific comparison depends on the tooling type, material, and application. AM supply chain for tooling is different from the conventional supply chain. The digitization of the tooling design promises to cut steps in the production process. Fast production of tooling is achieved when the required AM set-up is located close to the production floor. The same is true for use of AM to make short-run mold tooling. For production mold tooling made thru AM, many steps are still involved. The digital design tools necessary for AM result in fewer production steps.
Cost – AM created tooling is more cost-effective than traditional tooling for prototyping. AM to make jigs and fixtures is also more cost-effective. Especially because of the ability of AM to build complex geometries for holding parts with complex geometries.
Photo Credits - Diversified Plastics & EOS
Performance – AM can create more complex casting patterns or cores. Create conformal cooling channels within mold tooling for uniform heat distribution. For jigs and fixtures, production-related performance features can be customized within individual tools. For example, markings to identify replaced parts, orientation, and embedded features to ensure easy part alignment, clearing of debris, etc.
Performance Enhancement
AM can create new designs where complexity in materials and part geometry is leveraged for improved performance. Understanding of these parameters is often critical to justify AM as an end-use production technique. And, often comes also with reduced engineering and supply chain costs. These are the main parameters the industries have started to deploy. Still one can visualize further improvements as design innovation to expand the uses of AM beyond its current applications.
The below list summarizes the main performance parameters.
Geometry optimization – The use of AM to access a complex geometric design space allows optimization of part properties, such as strength to weight ratio, in a manner unachievable by methods such as machining and casting. The topology optimization applies a fixed set of constraints (e.g., material, joints, bounding box and mechanical requirements, etc.) to cut material consumption while maintaining or improving mechanical properties. The generated geometries often resemble organic structures and are only possible to be created using AM. In new methods, internal lattice structures can be re-distributed throughout the member to further optimize weight and strength otherwise rigid structure
Hollow cavities and channels – Internal channels and cavities can be designed as heat exchangers, which need maximum surface area contact between the fluid or gas. And, the heated block surrounding the material to enable more effective heat transfer. Linear geometries are less effective than surfaces that can form zig-zag shapes to increase surface area to maximize heat transfer.
Customized surface properties – AM can be used to make unique surface geometries. For example, lattice structures on the exterior of the part can be useful to aid bone ingrowth into medical implants. Specially created surface roughness may also be useful for heat exchange applications.
Design consolidation – AM can allow the design simplification of not only a single part but the entire assemblies. And, remove constraints that currently drive us to create separate parts. Complexity becomes simple in creating the consolidation of many assemblies into lesser parts. And, redesigning these fewer parts assemblies to leverage the design freedom of AM. Rather than, according to the constraints of conventional ways such as machining, molding, and casting. The part consolidation provides the most convincing proof of performance improvement. And, value addition in the entire engineering and supply chain costs.
Credits : General Motors, Autodesk
Part Production
AM is not cost-effective w.r.t conventional manufacturing when an equal design is considered. There are other advantages that can tilt the balance toward AM. Including complex parts which improved performance, customization, and time savings. Yet, when considering the choice of AM for the production of end-use parts, understanding the cost drivers of AM is very critical.
AM generally is cost-effective at lower quantities. Because tool-free production removes the need for fixed investment in tooling such (injection molding or casting die). But, the cost of AM parts is relatively unchanged as production quantities increase. This is not a flat curve, because some economies of scale can be achieved. So, as quantities increase, AM becomes less attractive as a production method than conventional manufacturing for a standard geometry. To overcome this cost hurdle, manufacturers must leverage the design freedom of AM to create better-performing or geometrically optimized parts.
The early adopters to use AM for production are in performance industries. Where the advantages given by AM in complexity, customization, or performance outweigh significant production cost premium. Not to mention the cost of acquiring AM expertise and confidence. Yet, there are already cases where AM is cost-effective without any major design changes. But this takes a specific business case, process selection, and production quantity.
Custom Parts
Customer-specific products are those which are made for the specific customer. Whereas customer specified products are those which are created to the desires and wishes of the specific customer. Example colour, texture, and surface finish. In both cases, customization takes place to achieve performance improvement. Whereas the latter case is oriented around involving the customer more deeply in the product design process.
Customization using AM requires a fully digital workflow to capture the customer's needs. And then translate these needs into the digital design for production. This may include high-resolution scanning, custom software, and manufacturing process constraints and limitations. Cost modelling tools must consider the difference introduced by changing dimensions, material specs, and related process parameters. Process controls and part approval plans must also consider the width of part attributes that may be produced.
Product customization and personalization are only beginning to be set up in the market. Customer-specific products are limited to medical devices and absorbed by fewer customers.
Spare Parts
The capabilities of AM for digitally-driven on-demand part production have important implications for the production of spare parts. And, the efficiency of maintenance and repair operations. There are four specific advantages of AM in the production of spare parts.
1. Spare parts can be produced on-demand. Using digital data with machines that can produce a wide variety of parts with specific materials, sizes etc. Considering the demand for spares is more difficult to predict than that for goods, as they are introduced into the marketplace. This means that important categories of waste are eliminated from the supply chain. For example, billions of dollars worth of automotive spare parts are held in the inventory. Additionally, the costs associated with the inventory, including the cost of land and labour to store and secure those parts. And, the depreciation of these parts over time.
2. Spare parts can be produced without tooling. This eliminates supply chain risk. For instance when the tool becomes damaged, or when a supplier discontinues the service of a product. In mass production, the high cost of tooling is amortized over volume sales, but with spare parts, this is not the case if a new tool must be made. The cost of re-installing tooling, even if kept in good condition, also increases the per-unit cost for a small production run. Increasing the price of aftermarket parts can compensate for the greater per-unit expenditure. But this discourages customers and decreases the firm's commitment to customer support.
3. Spare parts can be produced at different locations. Sharing digital data is far simpler than shipping a master tool for injection molding or casting. This is very important in resource-limited environments where continuous operation is essential. A similar way is applied to the defence sector, where continuous readiness is essential to operations.
4. AM can be used for on spot-repair of damaged components. Can be done without the need to fabricate an entirely new part. This is an application of DED-based metal AM processes. The advantages here are clear: parts can be repaired with limited material and without much manual labour. The same benefits mentioned above about the distribution of resources applies here as well. A part could be repaired closer to its point of use.
Hand brake lever photo credits: Markforged
Architecture
An extra dimension of AM, which reflects upon all industries. Yet is customer-facing, is the creative dimension of aesthetic and architectural design. While many of these examples come from fine art, high-end fashion, and home appliances, it is yet another important branch of the AM. These applications of AM also involve advanced software and computation and will enter the mainstream as a digitized lock into place.
3D printed jewellery photo credits: formlabs
Conclusion
Earlier Additive Manufacturing has been limited to the production of prototypes as a proof of concept etc. Now AM has come out of the prototyping era and slowly affecting a diverse set of industries across the spectrum. Henceforth, the future growth of AM is going to be driven by mass customization and tailored products for every need.
Blog created by - 3D SculpLab Team