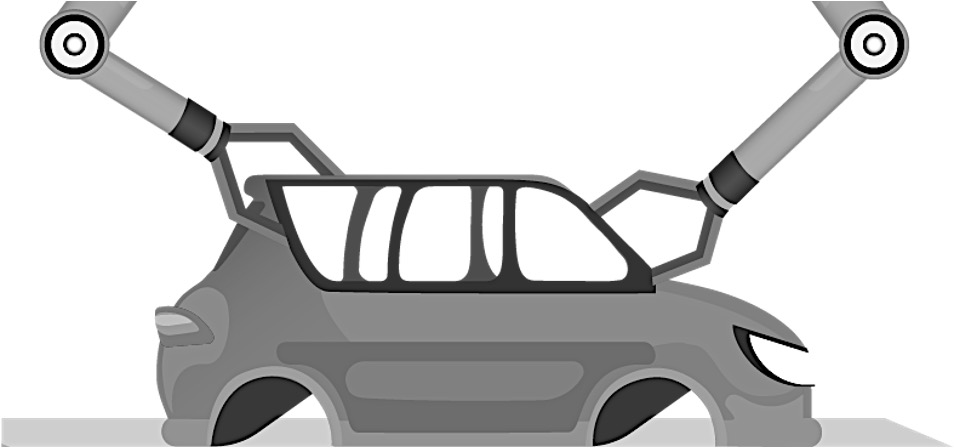
A design is considered to be the best if it contains fewer parts, use commonly available components, easy to manufacture and is easy to assemble. Also, a smaller bill of material(BOM) simplifies data management for organizations. For designers, design for assembly should be the key driver for any product development. The following blog talks about various tips to create a DoA be its injection molding, machining or 3D printing etc.
Identical parts
Generally, assemblies are created by using identical or symmetrical parts for the ease of manufacturing and assembly. Traditionally, two halves of an electronic housing, one-half bosses with self-tapping holes and the other half with thru-holes for screw mounting. This design will require a separate core cavity for injection molding or two different machined components. If the design is created in such a way that one half could be mounted on top of the duplicate copy, this way you’ll need to design only one-half saving money and time to market. Also, greatly simplifies the assembly process.
Self-alignment
By creating a self mating design introducing snap fits, designers can get rid of fasteners, washers, spacers etc eliminating the hand installation process. Additionally, can also apply snap hinges (ref image) for the easy installation step. This way the entire design is reduced to just one part, one core-cavity, one mold, compressed BOM, simplified assembly process. This will also make sure less production issues, easy part replacement during field servicing. For assembly, a simple holding fixture is needed, no special training for the operator and eliminates part alignment errors. Hinges can also be 3D printed in nylon if needed.
Family molds
An assembly consists of several individual parts joined together to create a design. An engineer would always try to design parts of similar shapes and sizes so that can be molded out of a single mold saving cost and time to manufacture. Another advantage of the family mold is that parts of an entire assembly could be created out instantly in a single material type hence all the parts are available at the same time for further processing.
Standard fasteners
Rather than designing nuts, bolts, hardware etc for a design, a designer should use off the shelf fasteners/hardware to save time and cost unless it is absolutely necessary to have special hardware. It is advisable to create a design around commonly available fasteners/hardware for large scale production volume simplifying the supply chain and inventory management.
Monoform design
Certain features could be directly incorporated into the design eliminating the need for a separate part to be assembled. For example, living hinges could be directly merged into the design and injection molded as a single part rather than separately mounting on the parts with fasteners. Polypropylene and ABS are some of the materials that are flexible and good candidates for hinges. Another example, the bottom legs of a typical domestic use washing machine could be molded along with the bottom tray instead of fixing separate legs plastic or metal. The bottom portion of a toy car including chassis, suspensions etc could also be molded out in a single. This way a complex multiple piece assembly is reduced to just part simplifying the bill of material, and assembly process. Designers only need to make sure the multi-feature single piece part is suitable according to the application environment.
Simplified assembly
In the case of multi-part design, emphasis should be more on the design which eases the assembly process be it manual or machine-driven. Parts should self align thru lugs, guide channels and poka yoke for a foolproof assembly process. Poka-yoke will ensure the parts are assembled as intended and there's no way it can go wrong or mismatch assembly. Use commonly available fasteners and make sure they all are accessible from the same side instead of rotating/turning the part, and all fastened by the same tool instead of different toolsets. Simplified assembly eases a lot of manufacturing and quality-related issues, reduces the burden on the operator, reduced the rate of rejection and make sure error-free design.
Insert and over-molding
Sometimes assembly contains components made from different materials to suit the application requirements. Fasteners, nuts, washers, pins etc can be easily insert molded into the mold eliminating the need for manual assembly. During assembly, an operator needs to just fasten some screws to create the final design. Designs also have flexible or rubber parts for grip or enhanced appearance. Rather than assembling separately, rubber parts can be over molded with different colour combinations and care must be taken that the selected material combination is chemically compatible. Hence insert and over molding saves extra manpower and extra processing cost for the company for large scale production over a period of time.
Liquid silicone rubber components
LSR is silicon derived polymer in two parts fixed together by a chemical bond. Its widely used for making molded parts across the industrial spectrum be it electrical, electronics, automotive and medical etc. Molded polymer when heat treated initiates a bonding reaction sequence. This reaction sequence provides everlasting strength and flexibility post-curing. The key advantages of LSR are excellent heat stability, retains flexibility at low temperatures, excellent resistance to chemical exposure, good electrical resistance. All these advantages make LSR the right material for seals, gaskets, O-rings etc reducing a designer's headache to great extent for performance demanding applications.
Other manufacturing processes
Manufacturing processes across industries are heading for major disruption and gone are the days when it took months and sometimes years to introduce a product into the market from concept stage to mass production. Technologies like 3D printing, hybrid manufacturing, IoT based manufacturing are a few of these. 3D printing is now slowly entering into the mass production lane which is at present dominated by conventional manufacturing technologies like injection molding and CNC. 3D printing can reduce the BOM from multiple parts to just one and can produce it a fraction of cost and time in comparison to traditional manufacturing. However, 3D printing is not going to entirely replace traditional manufacturing because some components still require traditional manufacturing for high precision manufacturing.
Conclusion
Design for assembly should be a rule book for every engineer when creating multipart assemblies. With fewer parts, it not only simplifies the downstream process like foolproof assembly, ease of packaging etc but also saves money for the organization. DoA can further enhance the quality and durability of the design which increase the overall productive life in real-world applications.
Blog created by - 3D SculpLab Team