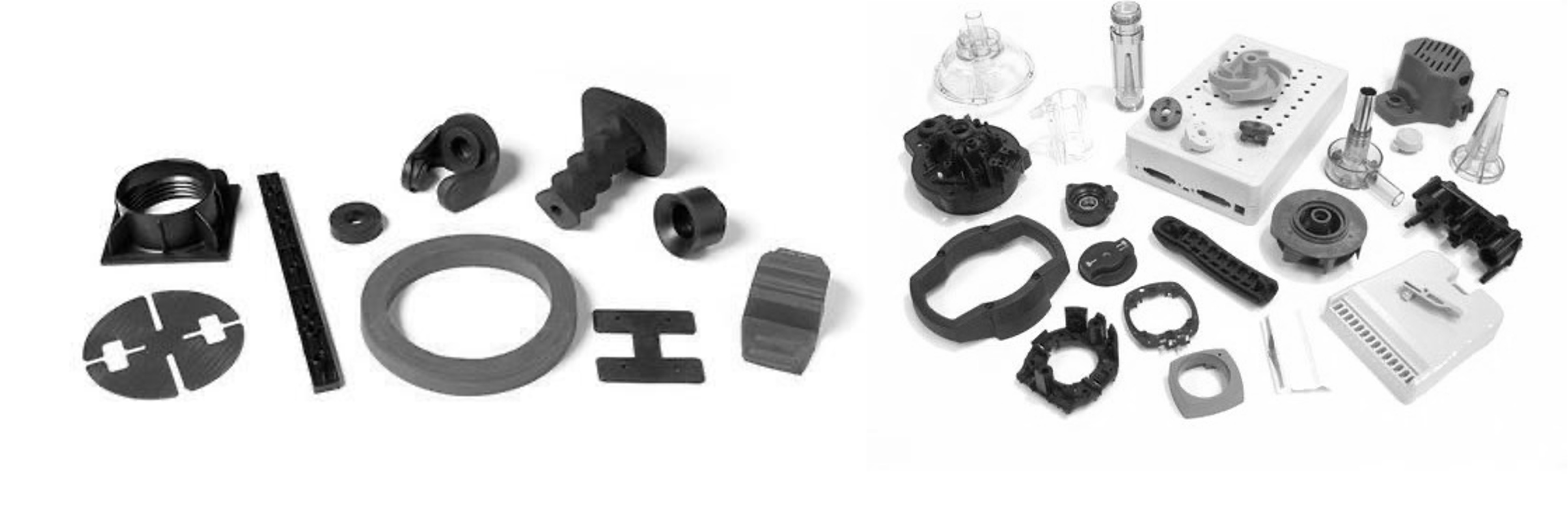
Overview
Cost is the most important factor before selecting any manufacturing process and reducing the costs. Organizations generally opt for large volume production to keep manufacturing costs low. Similarly, for injection molding, the cost per unit would be very high if volumes are low.
Injection molding appears to be more expensive than 3D printing & CNC machining, but the capability to expand production from a few hundred to millions of parts at a faster rate is unmatched with any other process. Establishing the cost of injection molding depends upon multiple factors like design complexity, type of surface finish, material selection etc.
Factors affecting the IM cost
- Remove undercuts
- Try not to have unwanted features
- Core & cavity strategy
- Minimize aesthetics and finishes
- Try for self-mating design
- Avoid post-machining mold changes
- Use DFM analysis
- Family molds
- Multi cavity molds
- Part size
- Use overmolding
Avoid undercuts
Avoid undercuts in design because it is the most important factor which affects the tool cost. Undercuts prevent or complicate the part ejection from the mold. If an undercut is needed, then create a design where a slider or side core could be applied. Mold costs could also be reduced by moving parting lines and draft angles enabling easier mold fabrication. Complicated mold designs not only increases the mold manufacturing costs also molded piece cost due to extended cycle time reducing the output.
Try not to have unwanted features
Features like textured surfaces, molded symbols/logos, molded texts, sentences increased the costs of mold fabrication.
Also, these features needed higher draft angles to enable error-free part ejection. These features are generally applied in automobile, medical and defence industries where part traceability is an important factor. It is recommended to use CNC compatible font sizes to keep fabrication costs impact to a minimum.
Core & cavity strategy
The vertical walls of enclosures and casings for electronics or electrical applications could be directly carved or sinked into the metal along with ribs. This will greatly simplify the tool construction, part ejection from the mold, surface finish of the part and save the tool from steep draft angles which will lower the overall tool fabrication cost. Suitable for tall walls and surfaces with ribs.
Minimize aesthetics and finishes
If not needed, the designer should avoid adding too much aesthetics to the part design. Surface textures, high gloss surface finish SPI-A1 push the tool cost upwards significantly. Designs requiring IMD (In Mold Decoration), IMF (In mold Film) and IML(In Mold Lamination) also escalate the costs significantly since these finishes complicate the tool design.
Try for self-locking design
If the designer is making an enclosure for electronics or electrical applications where two halves are needed to create an assembly, then the designer should make one half in such a way that another copy could easily snap-fits over each other in any direction. This way, only one core cavity is needed saving tool fabrication cost, time and a faster way to regular production.
Self-locking design
Avoid post-machining mold changes
Modifications to fabricated mold are sometimes difficult to incorporate and should be avoided. It is relatively easy to remove material from the carved metal but very difficult or impossible to add material. Material addition at a smaller level like filling rib cut or closing a small hole is possible by minor reworking. If the need arises to fill large material it's better to re-fabricate the entire core cavity. However, any reworking re-fabrication comes at an additional cost impact. It's better to take feedback from the toolmaker to avoid any tool re-working. You can also refer to 3DSculpLab’s injection molding design guide for more information.
Design For Manufacturing (DFM) analysis
A designer should keep in mind the tool manufacturability while creating any design. It's better to incorporate features and geometries that are easy to CNC machine and avoid non-machinable shapes & geometries. Features that require a special manufacturing setup are bound to have substantial cost impact and increased lead time.
Family molds
Parts of an assembly structure could be manufactured cost-effectively in a family mold type tool. Family mold is the tool design where multiple parts are injection molded at the same time. This reduces the need for separate molds for each part, hence, reducing the cost of tool fabrication and time to market.
Family mold made parts
Multi cavity molds
Multi cavity molds are those where the same core cavity is repeated to achieve a very high rate of production. The cavity number is carved on the tool surface to identify which part belongs to which cavity in case of tool troubleshooting.
Part size
A designer should also think about the part size which is going to be manufactured since this will have a negative cost impact. The part should fit inside the mold perfectly, adequate spacing for other tool-related features like spruce, runners, gating, ejector pins/ejector mechanism should be available.
Use over molding
Overmolding is a process of adding a plastic/rubber feature over an already injection molded part. Though overmolding is a cost addition option it will save the designer from the hassles of manually assembling the part by an operator where precision is key. Multicolour plastic toothbrushes are a perfect example of overmolding.
Conclusion
Injection molding is the most suitable technology for mass-market at the lowest possible cost and could achieve the rate of production from a few thousand to several million per annum. In today’s era where every penny counts, by following a few small design tips, a designer could save millions of dollars for any organization.
Blog created by - 3D SculpLab Team