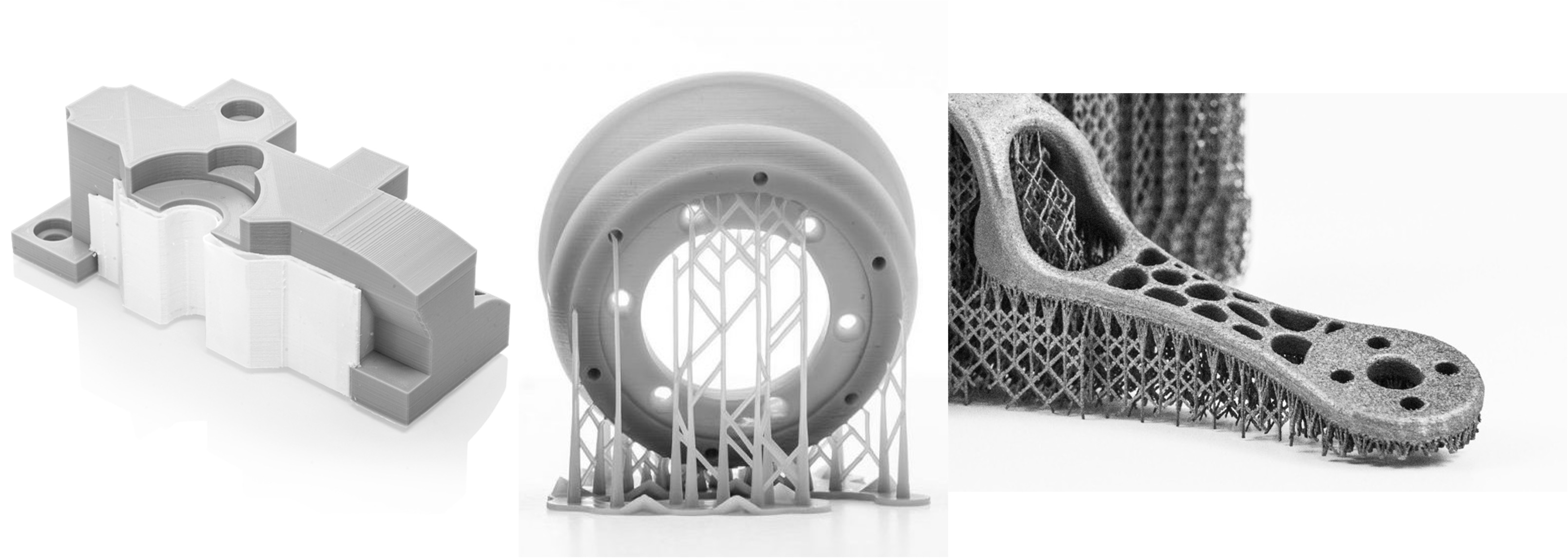
Support structures are an important feature of the 3D printing process. It helps in creating unsupported shapes/designs and complex geometries. Without support structures, it is impossible to realize the full potential of 3D printing and the freedom to design unconventional shapes. The support structure can be removed later during the post-processing of the 3D-printed part. Support structures can be created for plastic and metal parts according to the requirements. Also, there are various strategies to minimize or eliminate the need for support structures entirely by applying DfAM principles. Support is important to prevent deformation and other defects of the part during the printing process. Unique support materials are available which can be easily detached from the part without much effort leaving behind a smooth surface.
When are support structures needed?
3D printing is the process of creating the object layer-by-layer cross-section-wise. However, overhang or cantilever-type shapes need scaffolding-type support to enable their formation. Without the support structures, the cantilever-type shape will simply collapse within the part or deform making the physical non-usable. In metal 3D printing where high heat application is involved, support structures act as fins dissipating heat from the part to the environment preventing the part from accumulating residual stresses which leads to various quality issues.
Support structures
Support structures in various AM technologies
Supporting structures are applied in almost every 3D printing process. Let's discuss structures in various 3D printing processes.
FDM (Fused deposition molding)
The FFF/FDM process works by extruding the filament out of the nozzle and deposition it on the build plate. Part builds layer by layer in the vertical direction as per the CAD data. The overhang or bridge-type features generally need support to hold them into the desired position. Without support, the overhanging feature will simply deform or collapse. Support material could be the same as the printing filament or secondary material extruded thru the second nozzle only where support structures are needed. Later the support structures are removed manually using pliers etc. or immersed into a liquid(water) to dissolve the supports in case of water-soluble support material.
FDM/FFF support structures. Photo credits: Ultimaker
SLA (Selective layer sintering)
SLA process forms part by solidification of photo-sensitive liquid resin by the application of laser light. Each time the laser beam strikes a thin film of resin, it solidified and gets deposited on the build plate. In complex geometries, overhang structures needed support structures to hold the shape in the desired place.
SLA support structures. Photo credits: Formlabs
SLS (Selective layer sintering)
This powder bed-based 3D printing technology does not need support because the surrounding powder (Nylon) particles provide the necessary support for bridges or overhang features. Hence, simplifying the post-processing procedure and further enhancing the design freedom of the designer to create complex geometries.
SLS made part without the support structure. Photo credits: hp
SLM (Selective layer melting)
SLM generally refers to metal 3D printing and the design to be printed requires supports for two reasons, first to ensure the part is firmly tied up to the base plate and to provide support to bridge & overhang type features. Second, heat dissipation during part formation due application of high is involved. Metal powder particles are melted by the application of a high-intensity laser and fused together to create a shape. Thus, supporting structures are essential for successful printing.
Metal 3D printing support structures. Photo credits: Materialise
DED (Direct energy deposition)
DED like WAAM (Wire Arc Additive Manufacturing) is the 3D printing process of directly depositing the feedstock (wire or powder) on the build plate thru a nozzle to generate the shape. Some DED machine supports the six-axis degree of freedom resulting in a less likely need for support.
WAAM made part without the support structure. Photo credits: Lincoln Electric
How to minimize or eliminate the need for support?
Design
We can eliminate the supports entirely if the part is designed as per the DfAM principles for the respective 3D printing technology. This will immensely simplify the post-processing procedures, reduced material consumption, reduce production costs and fast turnaround time. Features, where the overhang angle is more than 45˚, can be produced without supporting structures. Any features protruding more than 3mm need a supporting structure to form. Hence, the designer needs to remember these points while creating the design for additive manufacturing.
Manufacturing
A skilled machine operator optimizes can still optimize the supporting structures by orientating the part in such a way that generated the minimum possible supporting elements. Supporting structures are generally auto-generated by the production or host software (Cura, simplify3D etc), however, some high-end software provide added functionality of customizing the supporting elements like addition, deletion or suppression of supports as per the requirements.
How are supports removed?
Supports are removed during post-processing of the printed part by using piers and other tools depending upon the geometry of the part. Some support is liquid soluble and can be dissolved in the respective liquid. Dissolvable supports are used to generate deep inaccessible cavities which are generally not visible from the outside. However, the operator needs to follow all the safety standard procedures while performing support removal activity. Metal 3D printing is followed by a multi-step post-processing procedure, part is initially heat treated in a furnace and then detached from the base plate by wire cut process. Then supports are removed manually using pliers etc. Once the supports are removed, they leave support marks over the surface which are removed by the means of sandpaper or machine grinding.
Support removing process. Photo credits: Novick
Video credits: Ultimaker
Key advantages of support structures
- The major advantage offered by the supporting structures is that they let the designer create complex shapes which cannot be done by conventional manufacturing like CNC machining, injection molding.
- Intricate and complex shapes can be realized easily with the help of 3D printing.
- Large overhang structures can be generated.
- Dissolvable support materials can create deep inaccessible cavities without worrying about how to remove support structures.
- Supports also ensure the part is firmly fixed to the build plate during the printing process.
Drawbacks
- Supports structure adds extra material costs to the 3D printed part along with the extra post-processing cost and increased turnaround time.
- Detaching support structures is a delicate procedure and needs a skilled person to do it without damaging the main part. Leftover support marks are removed by manual or machine sanding to achieve the desired surface finish.
- Support structures are auto-generated by the software and sometimes the software may or may not generate the support as per the requirement.
Conclusion
Supporting structures do let the designer develop complex products, however, improving the support structure design and its post-processing are some of the key hurdles in the entire 3D printing process. With continuous innovations, the industry is striving hard to get around the challenge. Further efficiency could be achieved by applying DfAM principles to the design itself and creating a support-free geometry. Support structures cannot be eliminated entirely from the process; hence it is up to the imagination of the designer to smartly create features requiring minimum supporting structures.
Future work
The current design philosophy is heavily skewed towards conventional manufacturing like CNC, injection molding, sheet metal etc, so, the designers are less likely to incorporate DfAM principles into their designs. Another challenge is the design created for 3D printing cannot be produced on conventional manufacturing setups. A present, 3D printing is not a cost-effective option for mass production requirements until AM systems are developed that can challenge conventional manufacturing price advantage for large-scale productions. Most industrial-grade AM systems are quite expensive, and small-scale organizations cannot afford them. Therefore, 3DSculpLab can support small organizations, and startups by manufacturing prototypes, low volume production at reasonable costs thru our online platform and delivering at your doorsteps. Reach out today for more information.
Blog created by - 3D SculpLab Team