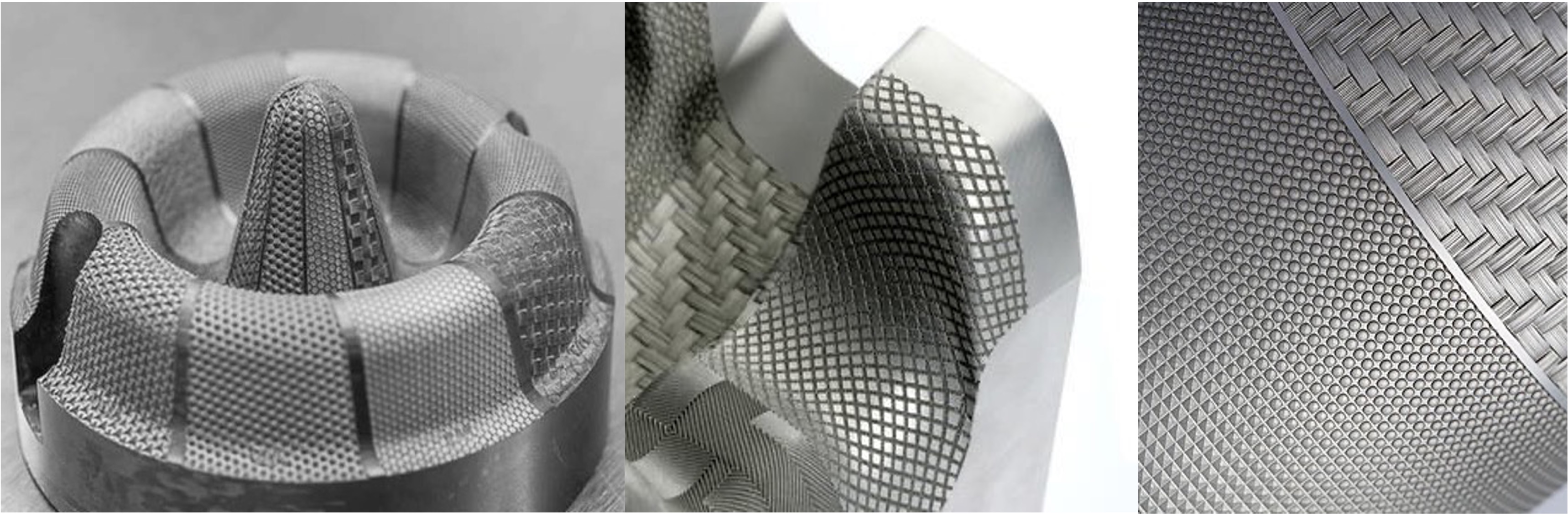
There are various ways to alter surface properties according to the requirements like sandblasting, itching, laser texturing etc. Laser texturing processes modify surface properties like roughness and textures by exposing the surface to high-intensity laser beams. Micropatterns are created on the surface of the material by removing the surface in very fine layers and with excellent repeatability. Typically, a laser beam scans the surface in linear, raster depending upon the surface pattern requirements like grooves, dimples etc.
This process is used to improve surface adhesion, weldability, wettability, friction, and thermal and electrical conductivity. For example, by texturing, the surface torque applied to the fasteners can be increased. Weldability between the two parts can also be increased by laser texturing.
How is laser texturing done?
Laser texturing is chipping away at the exposed surface by a high-intensity laser beam striking the exposed or target surface and altering the surface properties. By varying the machine parameters, we can customize the surface patterns, roughness etc according to the need. A rough surface pattern increases the adhesion property for adhesives by creating additional holding surfaces. The duration needed to chip off the surface by laser beam depends upon the kind of application/adhesion needed. Laser exposure time generally lasts for around 100 nanoseconds and laser output power depends upon the kind of surface exposed to it, type of pattern needed and roughness specifications.
Zero input process
Other surface treatment process like powder coating, Beed blasting, chemical etching and polishing etc needs input materials like chemicals, and polishing paper and span over several stages. On the other hand, laser treatment does not require any consumables resulting in lower process cost, does not need any special maintenance and enhances workplace safety for the operators. Handling of chemicals, and substances, and wearing of special safety gear are not needed making the entire process less complex, also, no recharge of consumables is required. A high level of automation makes the human-machine interface to a minimum. The system has inbuilt extraction of gases, fumes or smoke generated during the process hence making the whole process safe.
Application of laser texturing
- Cladding
- Thermal spraying
- Paint and other coatings
- Mechanical seals
Cladding
Laser cladding is the process of creating repeatable textures on the exposed surface to improve adhesion. This is done by directing a laser beam to the surface and melting the metal particles which are blown along the laser path from the nozzle creating a perfect surface for further operations. Other processes like beed/sand blasting may alter the surface properties but laser cladding does not cause such issues.
Laser cladding process
Thermal spraying
Laser surface texturing enhances the effectiveness of various spray coatings like cold spray and plasma spray by preparing the surfaces for the process. Laser texturing can generate patterns with very high accuracy and repeatability with exceptional quality surfaces needed for the surface treatment process. Surface roughness enhances the adhesiveness of the overlaying part/object and generates stronger holding forces between them. Also, it ensures optimal density and permeability of the substrate or coating.
For softer metals like copper, aluminium etc laser texturing is the best method than other techniques like abrasive blasting or chemical treatment which can cause surface defects like micro-cracks etc. Instead, laser texturing may increase the strength of the component by blocking the transmission path of cracks.
Thermal spray coating
Paint and other coatings
Paint adhesiveness can further be increased by creating a rough or wavy texture. On sheet metal parts, laser texturing is the best way to increase the paint's holding force onto the surface. Laser treatment cleans the exposed surface by removing particles that can cause contamination thereby increasing the bonding force between the paint coating and surface and also resists paint peeling off the surface.
Laser texturing is the best alternative to other surface treatment processes like abrasive blasting, electrical treatment etc prior to painting resulting in uniform paint quality across the parts.
Mechanical seals
Mechanical seals are designed to prevent leakage of the fluid from the endpoints of rotating shafts such as lubricating oil, pressure fluids etc. Seal performance depends upon the adhesiveness between the seal and the surface. Laser texturing can greatly improve the seal's performance by improving the surface adhesion by creating small dimple textures where the seals are exposed to elevated pressure and friction. Texturing greatly improves the seal's performance and durability by retaining fluids and lubricants.
Mechanical seals
Laser texturing on plastics
Laser-based Textures on the plastic parts not only enhance the aesthetics of the design but also the performance, enhanced grip, and patterns besides chemical-based texturing. Laser-based texturing is not only fast but also saves time and the operator from handling harmful chemicals and safety gear. There are two types of laser texturing on plastics, one is directly on the mold surface and the second is during the post-processing of plastic parts. In-mold decorations are created by exposing the mold surface to laser texturing. Patterns are directly engraved onto the mold surface and the same reflects on the molded plastic parts. The second process of laser texturing is to create signs, symbols, and text notes on the plastic parts. Wherever the laser strikes the plastic surface it burns and turns white. The created designs are long-lasting and do not get erased easily.
Laser texturing in mold. Photo credits: rmpc
Laser engraving of symbols
Conclusion
Laser texturing is a versatile process that saves time and effort. In comparison to chemical treatment, there are certain design and environmental benefits of laser texturing. No need for handling or refilling harmful chemical make the entire workplace safe for the operators and enables faster turnaround. Laser textures offer a high degree of customization according to user needs ranging from wood, leather, plastics, metals etc. Since laser texturing is an entirely digitally controlled process, it offers a high degree of repeatability and consistency to manufacturers across the regions. New design patterns can be created by laser texturing by advanced digital controls overcoming the limitations of chemical treatment.
Blog created by - 3D SculpLab Team